引言
鈦及鈦合金管具有比強度高、 耐高溫及耐腐蝕 等優(yōu)點, 已經(jīng)被廣泛應(yīng)用于航空航天、 石油化工和海
洋工程等領(lǐng)域[1-2]。 鈦及鈦合金具有滑移系少和 熱傳導(dǎo)系數(shù)小等特點, 因此鈦及鈦合金管在塑性變 形過
程中更容易產(chǎn)生尺寸不均勻和表面質(zhì)量差等缺陷。 目前, 鈦及鈦合金管的制造工藝主要有軋制[3]、 拉拔[4]、 擠壓[5]和旋壓[6] 等。 軋制工藝生產(chǎn)效率高, 但是容易造成管坯變形不均勻, 多用于鈦管的開坯。 拉拔和擠壓工藝生產(chǎn)流程簡單, 但生產(chǎn)道次多, 能量消耗大。 旋壓工藝具有加工精度
高、力學(xué)性能好等優(yōu)點, 但效率較低。
目前, 國內(nèi)外學(xué)者在鈦及鈦合金管材的制備工藝、 過程仿真及質(zhì)量控制等方面開展了許多研究工作。
尹業(yè)宏等[7]研究了軋輥輥形和軋制工藝對成形 鈦管表面質(zhì)量的影響規(guī)律, 進行了軋輥輥形和工藝參數(shù)合
理設(shè)計。 周大地等[8] 研究了穿孔過程中管坯 中心孔腔形成機理和應(yīng)力應(yīng)變場分布, 在兩輥斜軋穿孔機
上穿軋出Ti80鈦合金無縫管。 ZHANGZ等[9]采用旋轉(zhuǎn)穿孔工藝研究了鈦合金厚壁管塑性成 形工藝, 基于控制變量法解決了旋轉(zhuǎn)穿孔過程中軋 卡和溫升嚴重兩個關(guān)鍵問題。 謝林均等[10] 研究了擠壓速度對熱擠壓成形TA16鈦合金管材組織、 力學(xué) 性能、 壁厚偏差及表面質(zhì)量的影響, 發(fā)現(xiàn)擠壓速度 降低使得管材成形質(zhì)量得到改善。 DAMODARAND等[11]利用有限元法模擬了鈦合金熱擠壓變形全過 程, 分析了擠壓速度、 初始溫度和模具結(jié)構(gòu)對鈦合 金擠壓變形過程的影響。 EBRAHIMIM 等[12]研究了進給速度、 主軸轉(zhuǎn)速和減薄率對旋壓成形純鈦無縫 薄壁管表面質(zhì)量和幾何精度的影響。 對于鈦合金管 材成形的新工藝, 于輝等[13-14]提出了管坯擠軋成形 工藝, 研究了小型管坯擠軋成形裝置和成形方法。
對于鈦合金管材成形的新工藝, 本課題組提出 了管坯擠軋成形工藝, 研究了小型管坯擠軋成形裝 置和
成形方法[13-14], 該工藝綜合了三輥斜軋成形和 旋壓成形的優(yōu)點, 本文以TA2鈦管為研究對象, 探 究管
坯在擠軋成形中的變形過程以及軋輥送進角、軋輥公轉(zhuǎn)速度和管坯前進速度對擠軋成形后管坯尺 寸精度的
影響規(guī)律, 獲得TA2鈦管擠軋成形的優(yōu)化 工藝, 并進行試驗驗證。
1、管材擠軋成形有限元模型建立
1.1幾何模型建立
本文采用 ABAQUS 有限元仿真軟件建立TA2鈦管擠軋成形有限元仿真模型, 如圖 1 所示。 圖 1a 為
管材擠軋成形的幾何模型, 主要由軋輥、 芯棒、 鈦管和推桿組成,TA2鈦管毛坯尺寸為 Ф12mm×2mm×
70mm (直徑×壁厚×長度)。 軋輥輥形由入口錐、均整段和出口錐組成, 入口錐和出口錐處存在入口錐成形
角 β1 和出口錐成形角 β2 , 軋輥輥形如圖 1b所示。 3 個軋輥圍繞軋制中心線按 120°均勻分布,軋輥
軸與軋制中心線之間存在送進角 α。 芯棒在變 形區(qū)內(nèi)固定不變, 對管坯內(nèi)壁起約束作用。 為了與 實際
擠軋成形過程中軋輥和推桿運動情況相一致,分別設(shè)定了軋輥公轉(zhuǎn)速度和推桿速度, 軋輥繞軋制 中心線公轉(zhuǎn)
, 推桿推動管坯前進。 管坯被推桿送進 變形區(qū)后, 由于軋輥與管坯接觸過程的摩檫力作用,軋輥做自轉(zhuǎn)運
動, 軋輥每繞軋制線轉(zhuǎn)動一次, 管坯 在前進過程中被加工一次。
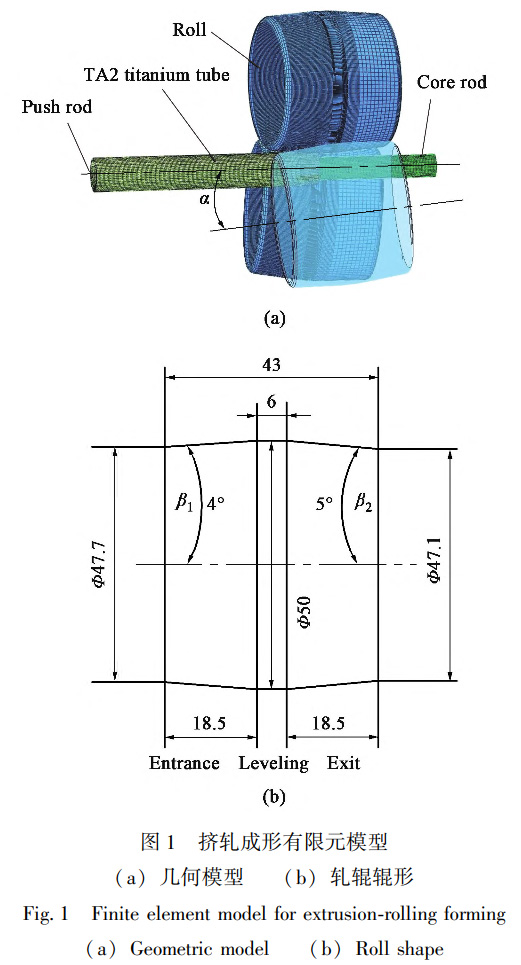
在擠軋成形過程中, 管坯發(fā)生塑性變形, 定義為可變形實體, 選用C3D8RT三維熱力耦合分析單元,
并采用任意拉格朗日歐拉 (Arbitrary Lagrangian Eulerian, ALE) 自適應(yīng)網(wǎng)格進行網(wǎng)格劃分, 防止管坯
在變形過程中發(fā)生網(wǎng)格畸變影響模擬計算。 軋輥、芯棒和推桿在成形過程中幾乎不發(fā)生變形, 因此 定義為
剛體, 劃分剛體單元R3D4。 為了保證鈦管擠軋成形有限元模型的準確 性, 管坯劃分為43200個單元
, 軋輥劃分為11408 個單元, 芯棒 劃分為 6611個單元, 推桿劃分為 1224 個單元。
1.2 工藝參數(shù)設(shè)定
在鈦管擠軋成形過程中,TA2鈦管的材料本構(gòu)方程和熱物理性能參數(shù)見文獻 [15] 和文獻 [16]。在鈦
管擠軋成形過程中, 表面的相互作用類型選用罰接觸, 管坯與軋輥、 芯棒以及環(huán)境發(fā)生熱傳遞。 TA2鈦管
擠軋成形的工藝參數(shù)如表1所示。
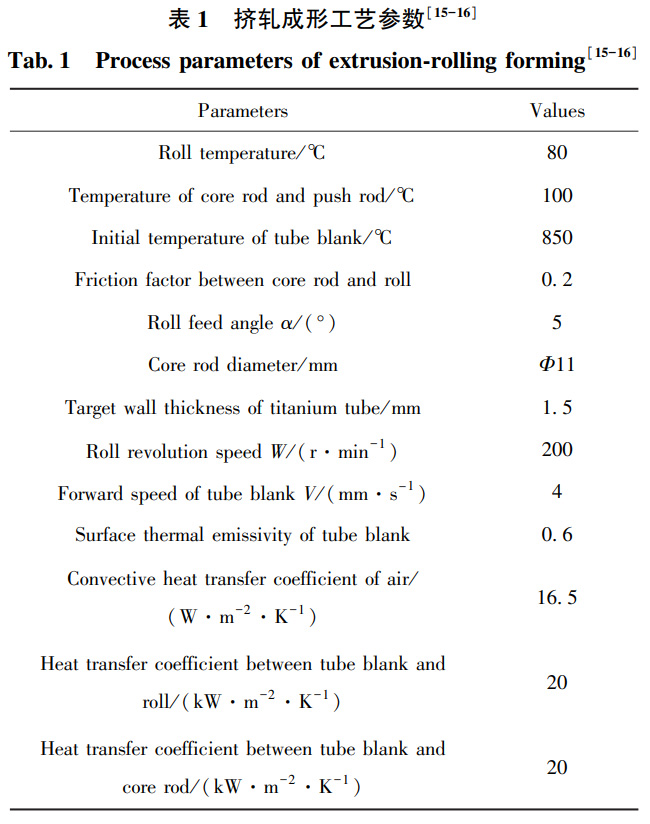
2、仿真結(jié)果和分析
2.1 管坯變形過程分析
對TA2鈦管擠軋成形有限元模擬結(jié)果進行塑 性應(yīng)變分析, 研究管坯的同一軸向截面在擠軋變 形區(qū)內(nèi)
不同階段的徑向應(yīng)變、 圓周應(yīng)變以及軸向 應(yīng)變的變化情況, 從而探究鈦管在擠軋工藝中的變形過程。
圖 2 為管坯不同階段的徑向應(yīng)變變化情況。 由 圖 2a 可知, 入口階段的管坯進入擠軋變形區(qū), 管坯
在徑向方向上受壓縮, 在 3 個軋輥作用下, 管坯的徑向應(yīng)變呈明顯三角分布, 最大的徑向應(yīng)變出現(xiàn)在軋
輥與管坯接觸部分。 由圖 2b 可知, 管坯進入軋輥 均整段, 徑向應(yīng)變隨著擠軋過程的進行逐步增大并由
管坯外表面向管坯內(nèi)表面滲透, 徑向應(yīng)變變化趨于穩(wěn)定, 徑向應(yīng)變由外向內(nèi)呈階梯分布。 由圖2c可知,
管坯脫離軋輥完成擠軋, 管坯徑向變形整體為 壓縮變形, 徑向變形量由外壁向內(nèi)壁逐漸減小。
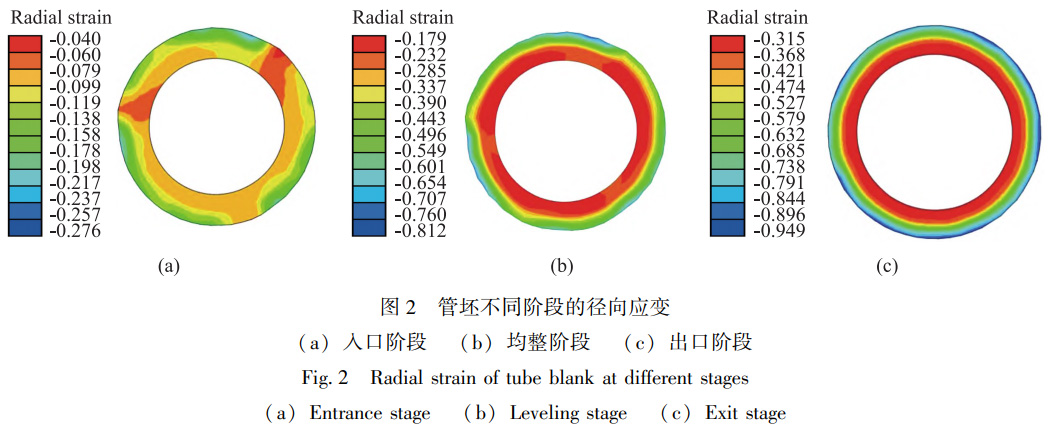
圖 3 為管坯不同階段的圓周應(yīng)變變化情況。 由 圖 3a 可知, 管坯進入擠軋變形區(qū), 圓周應(yīng)變呈明顯
三角分布, 最大圓周應(yīng)變出現(xiàn)在外表面, 圓周應(yīng)變 基本為正值。 由圖 3b 可知, 管坯在軋輥均整段作用
下均整壁厚, 隨著管坯在擠軋變形區(qū)內(nèi)變形, 圓周 應(yīng)變的三角分布效應(yīng)逐漸減小, 圓周應(yīng)變變化趨于 穩(wěn)定
, 圓周應(yīng)變基本由外向內(nèi)呈階梯分布。 由圖 3c可知, 管坯脫離軋輥完成擠軋, 管坯圓周變形整體 為拉伸
變形, 圓周變形量由管坯的外壁向內(nèi)壁逐漸 減小。
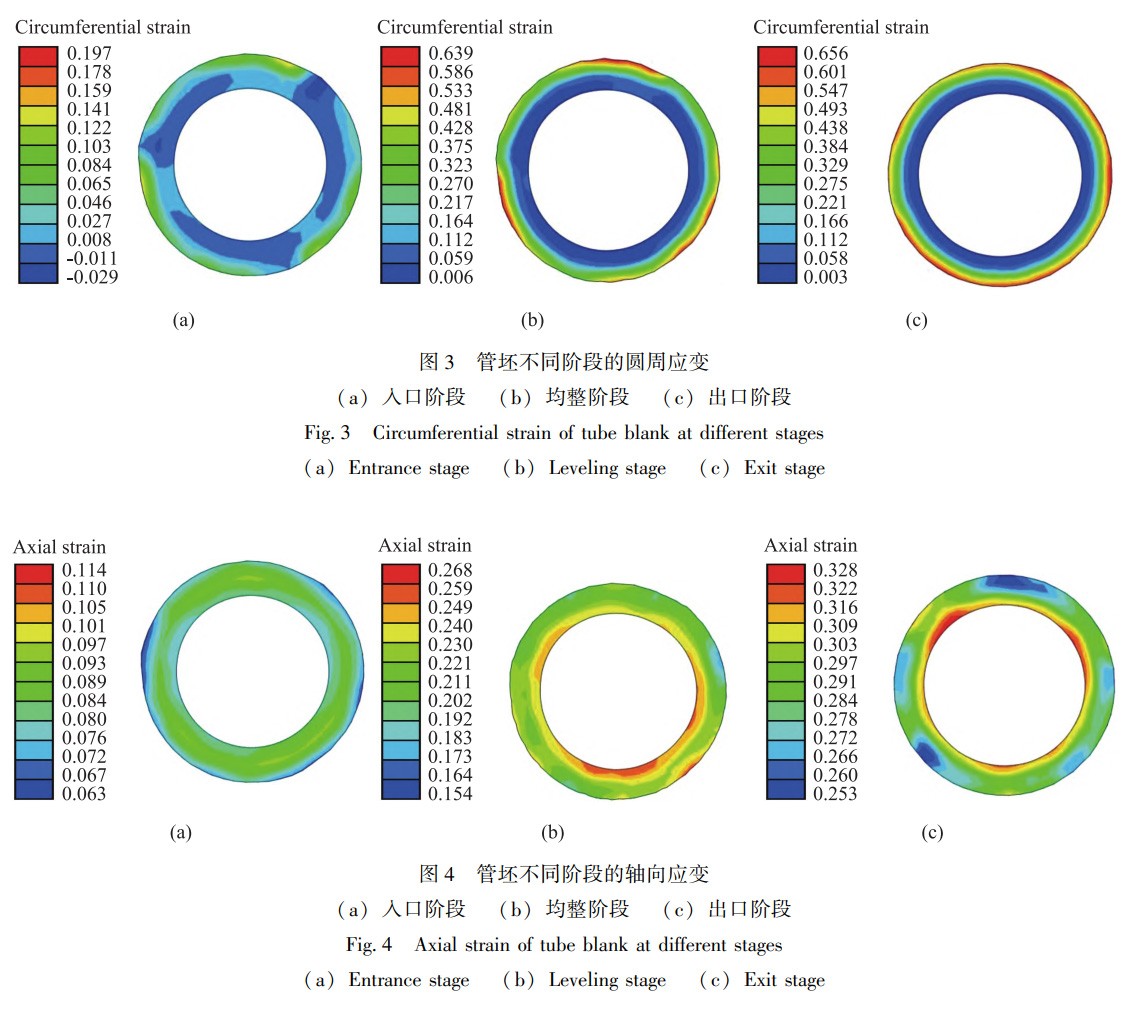
圖 4 為管坯不同階段的軸向應(yīng)變變化情況。 由圖4a可知, 管坯進入擠軋變形區(qū), 軸向應(yīng)變基本為
正值, 表明管坯截面受徑向壓縮的影響在軸向上呈 現(xiàn)拉應(yīng)力狀態(tài), 管坯伸長。 由圖 b可知, 管坯在軋
輥均整段作用下均整壁厚, 軸向應(yīng)變變化趨于穩(wěn)定。
由圖 4c 可知, 管坯脫離軋輥完成擠軋, 管坯軸向變形整體為拉伸變形且呈三角形分布。
2.2 送進角對管坯尺寸精度的影響
為了研究管坯的尺寸精度, 對擠軋成形有限元 模型的管坯節(jié)點進行預(yù)處理, 如圖 5 所示。 徑向截 面
定義示意圖如圖 5a 所示, 在網(wǎng)格中將需要進行 對比研究的節(jié)點定義為內(nèi)部集合, 內(nèi)部集合依次 分為擠軋
初始變形區(qū)、 擠軋穩(wěn)定變形區(qū)和未擠軋 成形區(qū), 在穩(wěn)定擠軋變形區(qū)依次定義 125 個間隔 相等的截面。
第 i 截面的周向節(jié)點示意圖如圖 5b 所 示, 在管坯截面外表面和內(nèi)表面各選取 20 個節(jié)點,分別定義為節(jié)
點集合 tw i 和 tn i。 編號 1~20 為管坯外 表面半徑測量點, 點到軋制線距離為管坯軸向某一截面外表
面半徑值; 同理, 編號 21 ~ 40 為內(nèi)表面半 徑測量點, 點到軋制線距離為管坯軸向某一截面內(nèi) 表面半徑
值。
由此得到的管坯外表面平均半徑計算公式, 如 式 (1) 所示。

式中: Rij 為管坯第 i 個截面第 j 節(jié)點外表面半徑,i = 1, 2, 3……125; j = 1, 2, 3……20。
同理得到管坯內(nèi)表面平均半徑計算公式, 如式(2) 所示。
式中: rij 為管坯第 i 個截面第 j 節(jié)點內(nèi)表面半徑。
管筒形工件成形質(zhì)量主要通過內(nèi)外表面半徑、壁厚、 壁厚偏差、 橢圓度及擴徑量進行評價, 管坯壁
厚偏差為壁厚最大值減去壁厚最小值, 是對管坯 壁厚均勻性的反映; 橢圓度為管坯外表面半徑最大值減去
半徑最小值, 是對管坯外表面成形質(zhì)量的反 映; 擴徑量為管坯內(nèi)表面半徑平均值與工件內(nèi)表面理論半徑
之差,是對管坯內(nèi)表面成形質(zhì)量的反映[17-18]。
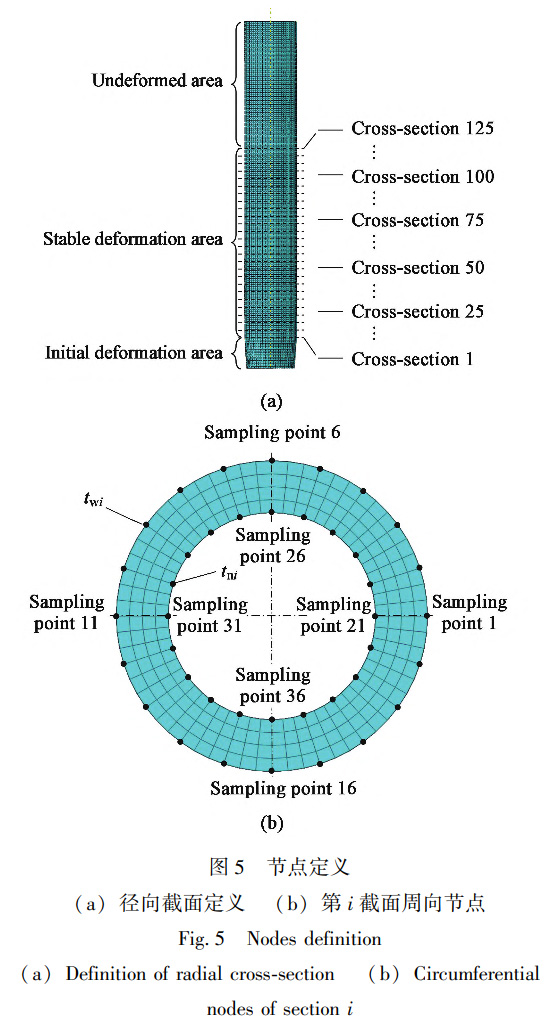
在管坯擠軋成形過程中, 送進角對管坯表面質(zhì) 量有著重要影響, 送進角選取不當, 會對管坯成形 表面
造成不同形式損傷。 在分析送進角 α 對管坯成 形質(zhì)量影響時, 軋輥公轉(zhuǎn)速度 W = 200r·min-1, 管 坯
前進速度 V = 4mm·s-1, 對不同水平送進角 α (0°、 1°、 2°、 3°、 4°、 5°、 6°
、 7°、 8°和 9°) 進行 模擬仿真。
不同送進角下管坯尺寸精度變化情況如圖 6 所 示。 由圖 6a 和圖 6b 可知, 管坯外表面半徑與內(nèi)表
面半徑隨送進角增大呈現(xiàn)先減小后增大趨勢, 送進 角為 6°時的管坯外表面半徑最小, 送進角為 4°時的
管坯內(nèi)表面半徑最小, 內(nèi)外表面半徑基本大于理想 值。 由圖 6c 可知, 管坯壁厚隨送進角增大呈現(xiàn)先增
大后減小再增大趨勢, 當送進角為 6° 時, 壁厚最 小, 壁厚均小于理想值。 由圖 6d 可知, 管坯壁厚偏
差隨送進角增大呈現(xiàn)先減小后增大再減小趨勢, 管 坯橢圓度與擴徑量隨送進角增大呈現(xiàn)先減小后增大 趨勢
, 當送進角為 4°時, 管坯的壁厚偏差、 橢圓度 和擴徑量達到最小值。 這是因為送進角直接影響軋 輥與
管坯接觸區(qū)的相對速度矢量和接觸面積, 從而 影響管坯在擠軋過程中的金屬流動。 送進角過大會 造成管
坯金屬材料過度變形, 降低擠軋過程穩(wěn)定性,降低管坯尺寸精度; 送進角過小會使軋輥與管坯變形區(qū)接觸長
度過大, 阻礙管坯變形區(qū)金屬軸向流動。
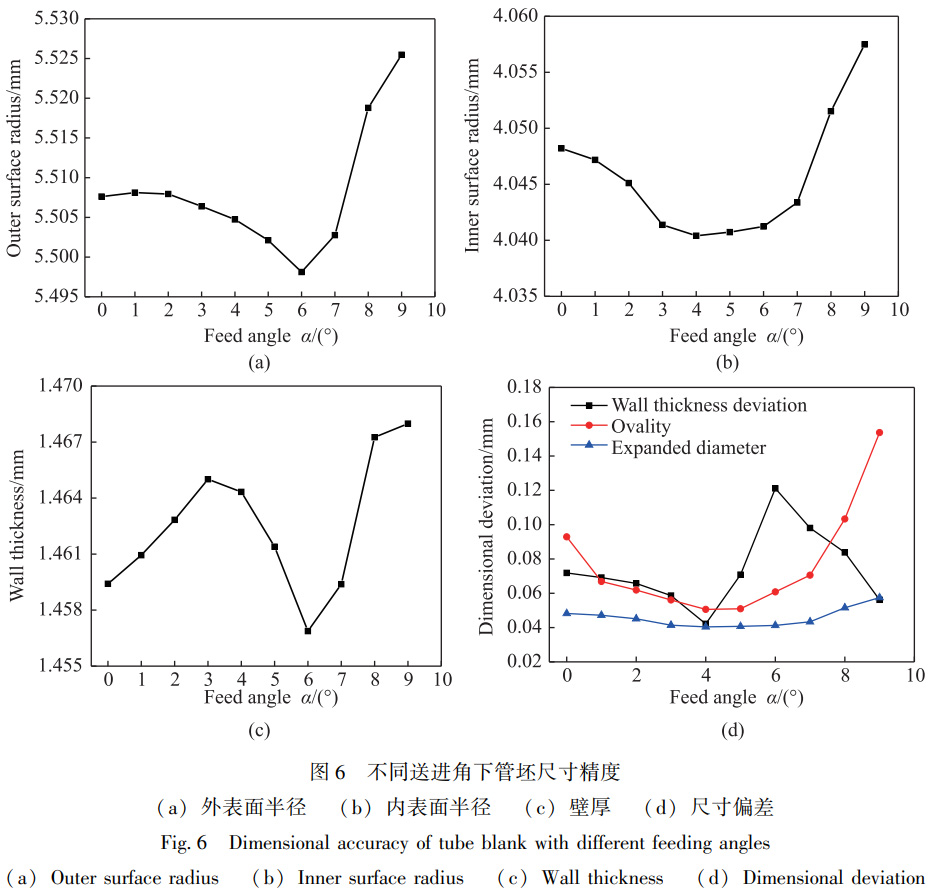
采用合適的送進角才可以使得管坯變形金屬流動均 勻, 管坯內(nèi)外表面半徑趨于理想值, 管坯壁厚偏差
、橢圓度和擴徑量減小。
2.3 軋輥公轉(zhuǎn)速度對管坯尺寸精度的影響
不同軋輥公轉(zhuǎn)速度對擠軋成形管坯表面質(zhì)量有 著不同影響, 合適的轉(zhuǎn)速可以改善管坯表面質(zhì)量。
分析軋輥公轉(zhuǎn)速度 W 對管坯成形影響時, 選取送進 角 α= 5°, 管坯前進速度 V = 4mm·s-
1, 對不同軋 輥公轉(zhuǎn)速度 W ( 100、 150、 200、 250、 300、 350、 400 和 450r·min-1) 進行
模擬仿真。
不同軋輥公轉(zhuǎn)速度下管坯尺寸精度變化如圖 7所示。 由圖 7a 可知, 管坯外表面半徑隨軋輥公轉(zhuǎn)速 度
增大而減小, 最小值為 5.435mm。 由圖 7b 可知,管坯內(nèi)表面半徑隨軋輥公轉(zhuǎn)速度增大先減小后增大,當軋
輥公轉(zhuǎn)速度為 150r·min-1 時, 管坯內(nèi)表面半 徑最小為 4.035mm, 內(nèi)表面半徑基本大于理想
值。
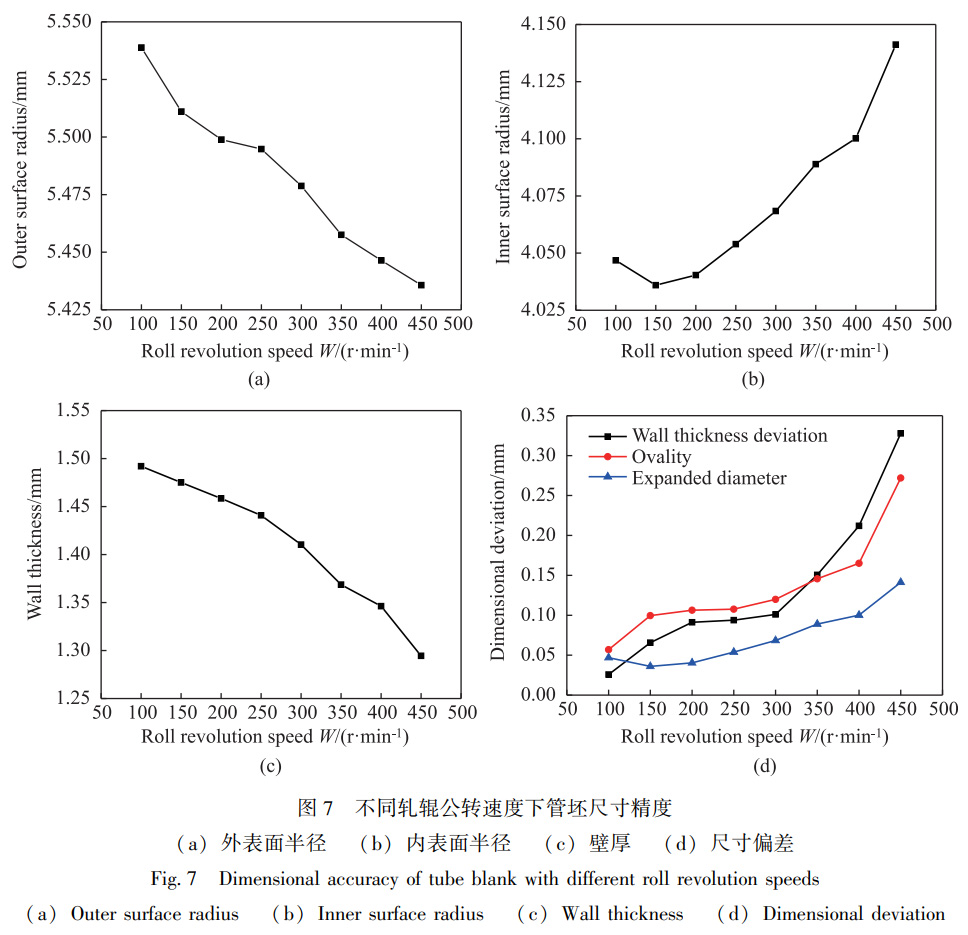
由圖 7c 可知, 管坯壁厚隨軋輥公轉(zhuǎn)速度增大而減 小, 最小值為 1.28mm, 管坯壁厚基本小于理想值
。
由圖 7d 可知, 管坯壁厚偏差、 擴徑量和橢圓度整體 上隨軋輥公轉(zhuǎn)速度增大逐漸增大。 這是因為軋
輥公 轉(zhuǎn)速度直接影響軋輥與管坯接觸區(qū)的相對速度矢量,進而影響擠軋過程中材料流動。 合適的軋輥公轉(zhuǎn)
速 度會使管坯表面成形質(zhì)量得到提高, 有效限制管坯 周向流動, 減小擴徑現(xiàn)象。 但軋輥公轉(zhuǎn)速度過大時,
軋輥和管坯接觸區(qū)的相對速度矢量過大使得材料塑 性變形能力降低, 管坯變形不穩(wěn)定, 尺寸精度降低。
2.4 管坯前進速度對管坯尺寸精度的影響
管坯前進速度不僅直接影響擠軋生產(chǎn)加工效率,而且與管坯尺寸精度、 表面光潔度有密切關(guān)系。 分析
管坯前進速度 V 對管坯擠軋成形影響時, 選取送進角α= 5°, 軋輥公轉(zhuǎn)速度 W = 200r·min-1, 對不同管
坯 前進速度 V (1、 2、 3、 4、 5、 6、 7、 8 和 9mm·s-1)進行模擬仿真。
不同管坯前進速度下管坯尺寸精度變化如圖 8所示。 由圖 8a 和圖 8b 可知, 管坯前進速度增大使 得
管坯外表面半徑和內(nèi)表面半徑先減小后增大, 管 坯外表面半徑和內(nèi)表面半徑最小值分別在管坯前進 速度為
3 和 4mm·s-1 時。 由圖 8c 可知, 隨著管坯 前進速度增大, 管坯壁厚先增大后減小, 當管
坯前 進速度為 5mm·s-1 時, 管坯壁厚最大。 由圖 8d 可 知, 當管坯前進速度大于
3mm·s-1 時, 管坯壁厚 偏差和橢圓度變化趨于平穩(wěn), 管坯擴徑量先減小后 增大。 管坯前進
速度過小不僅會使擠軋生產(chǎn)效率低,而且會導(dǎo)致管坯在單位時間內(nèi)受到軋輥更多軋制,管坯成形質(zhì)量變差。
管坯前進速度過大會使管坯在 軋輥均整段不能得到充分擠軋均整壁厚, 管坯壁厚 不均勻, 擴徑量增大。
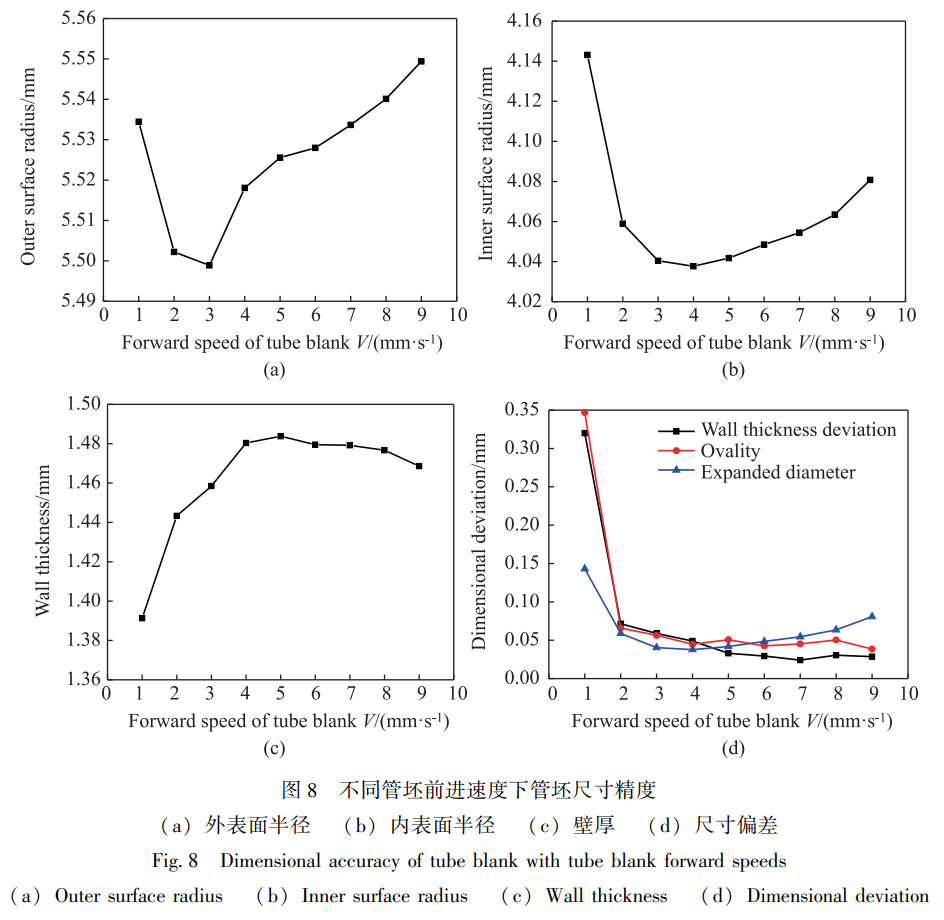
2.5 擠軋成形工藝優(yōu)化
TA2鈦管擠軋完成后的管坯外表面半徑、 內(nèi)表面 半徑和壁厚的目標值分別為 5.5、 4 和 1.5mm。
根據(jù) 本文 2.2 節(jié)~2.4 節(jié)單個工藝因素對TA2鈦管擠軋成 形影響分析, 選用合適的工藝參數(shù)進行正交
試驗, 得 出最優(yōu)工藝, 正交模擬試驗參數(shù)如表 2 所示。
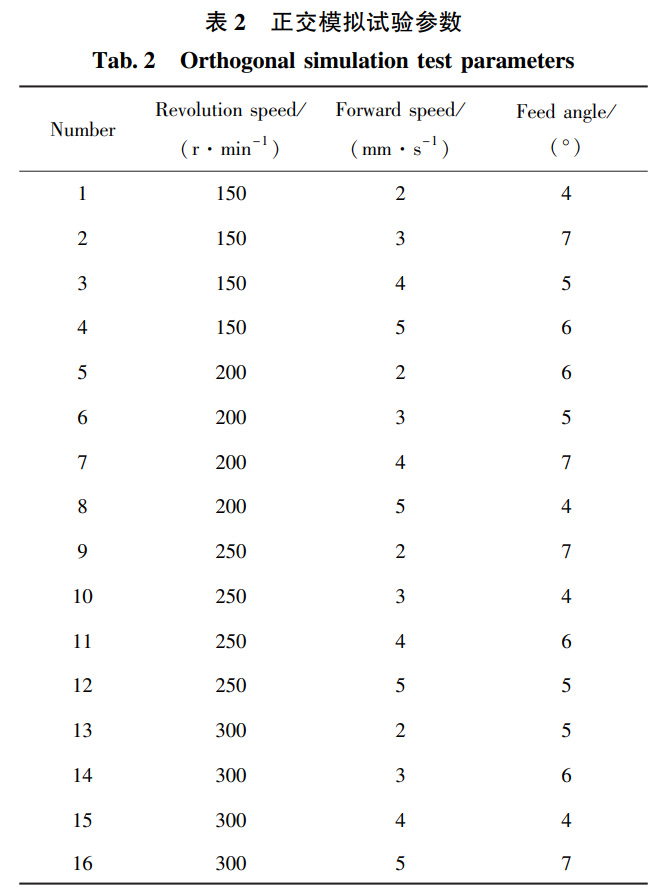
第 9 組正交模擬試驗管坯擠軋發(fā)生嚴重扭轉(zhuǎn)變 形, 對剩下 15 組模擬結(jié)果進行管坯表面尺寸精度分
析, 得到管坯穩(wěn)態(tài)擠軋區(qū)內(nèi)的管坯尺寸質(zhì)量如圖 9所示。
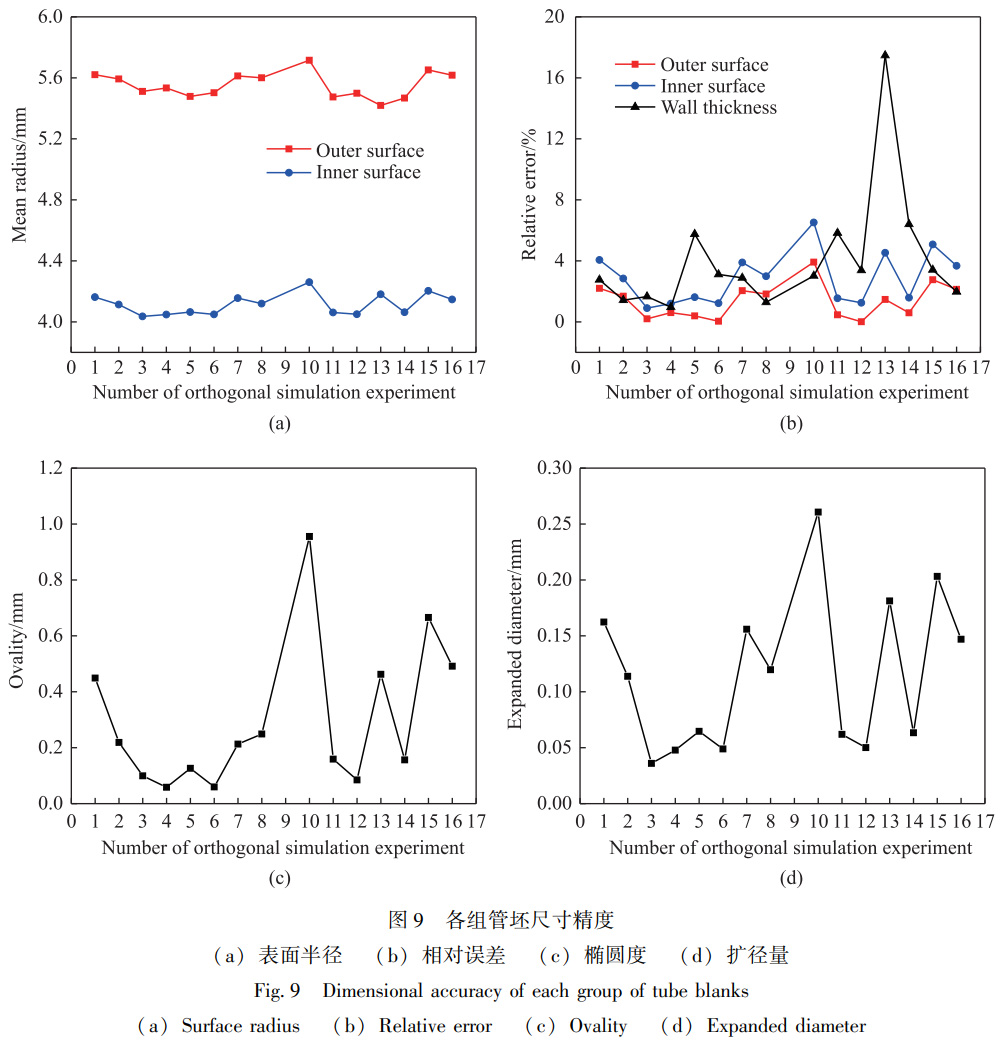
通過對圖 9 分析可得, 第 4 組模擬結(jié)果與目標值 最為接近, 外表面半徑相對誤差為 0.61%, 內(nèi)表面
半 徑相對誤差為 1.20%, 壁厚相對誤差為 0.96%, 而且 橢圓度為 0.0585mm, 擴徑量為 0.0478mm。
因此, 通過正交試驗優(yōu)化得到擠軋成形的工藝 參數(shù)分別為軋輥公轉(zhuǎn)速度 W = 150r·min-
1, 管坯前 進速度 V = 5mm·s-1, 軋輥送進角 α= 6°。
3、試驗驗證
采用上文優(yōu)化得到的工藝參數(shù)在擠軋成形設(shè)備 上進行擠軋成形試驗, 對擠軋成功后的TA2鈦管進 行
尺寸精度測試和分析, 驗證有限元模型的準確性 和鈦管擠軋成形的可行性。 本試驗采用寶雞泰諾達金屬材
料有限公司拉拔退火生產(chǎn)的TA2鈦管, 管坯 規(guī)格 ( 直 徑 × 壁 厚 × 長 度) 為 Ф12mm × 2mm ×
70mm。TA2鈦管擠軋成形有限元模擬中管坯初始 溫度設(shè)為 850℃ , 但實際擠軋過程中需要耗費一定 時間
把管坯從加熱爐搬運到擠軋成形設(shè)備上, 導(dǎo)致 管坯擠軋初始溫度有所下降, 所以將管坯加熱爐以
50℃·min-1 加熱到 870℃ 后保溫 40min。TA2鈦管擠軋試驗在自主研發(fā)設(shè)計的擠軋成形設(shè)備上完成,管
坯加熱完成后送入擠軋成形設(shè)備導(dǎo)向筒, 液壓推 桿推動管坯與軋輥和芯棒接觸進行擠軋成形。 截取 管坯
穩(wěn)定擠軋段如圖 10 所示, 在高溫下TA2鈦管與空氣接觸發(fā)生氧化反應(yīng), 在管坯表面形成白色氧 化物, 擠
軋后的管坯表面質(zhì)量良好, 壁厚均勻。
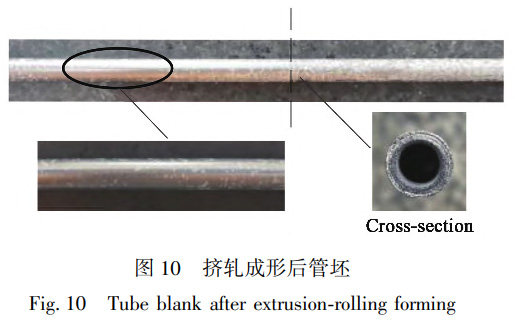
分別測量成品管穩(wěn)定擠軋段頭部、 中部和尾部尺 寸, 如表 3 所示。 由表 3 可知, 擠軋得到的TA2
鈦管 外徑偏差為 0.12mm, 內(nèi)徑偏差為 0.06mm, 壁厚 偏差為 0.05mm, 滿足標準 GB / T3624—2010
[19] 中 相應(yīng)尺寸允許偏差, 證明了所建立的TA2鈦管擠軋 成形有限元仿真模型的準確性。 為分析擠軋
成形后 管坯壁厚的均勻性, 測量擠軋成形后管坯環(huán)向一 周和同一母線處的壁厚, 如圖11所示。 由圖11可
知, 管坯環(huán)向一周壁厚的最大差值為 0.8mm, 管坯 同一母線處壁厚的最大差值為 0.06mm, 證明了擠 軋
成形后管坯壁厚的均勻性。
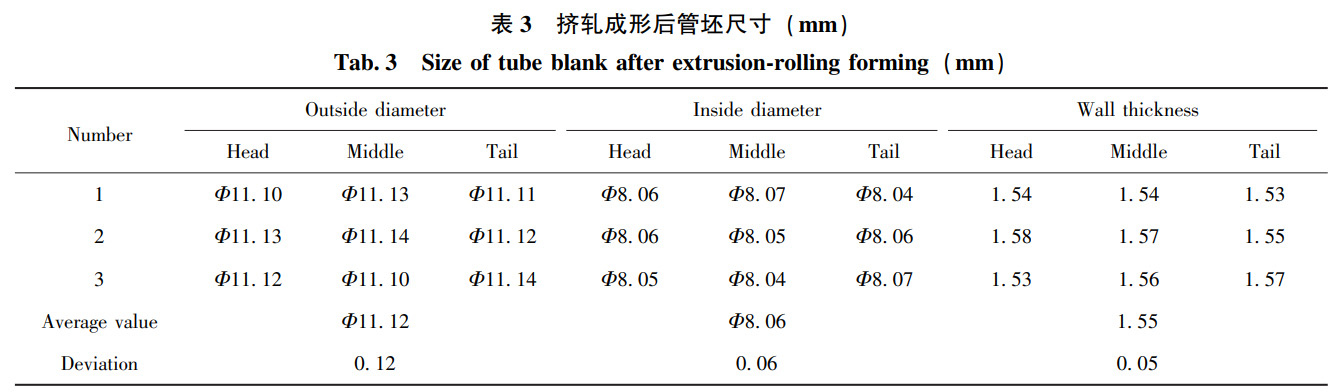
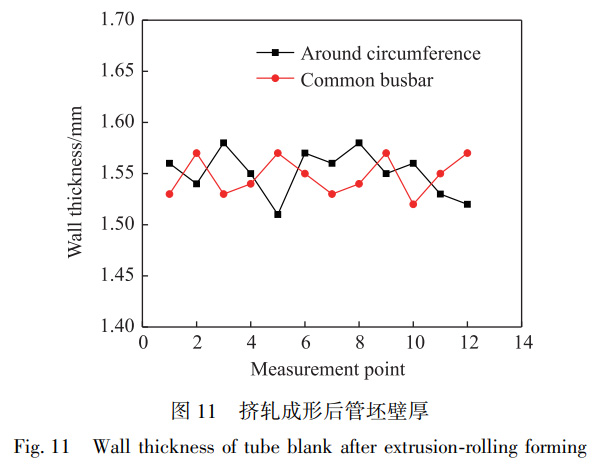
4、結(jié)論
(1) 在擠軋變形開始階段, 管坯的徑向應(yīng)變、周向應(yīng)變以及軸向應(yīng)變呈明顯三角分布。 隨著擠 軋變形
進行, 徑向應(yīng)變、 圓周應(yīng)變以及軸向應(yīng)變 逐步增大并由管坯外表面向管坯內(nèi)表面滲透, 徑 向應(yīng)變和圓周
應(yīng)變的三角分布效應(yīng)逐漸減小, 管 坯在軋輥均整段的徑向應(yīng)變和圓周應(yīng)變由外向內(nèi) 呈階梯分布。 (2) 送
進角有利于管坯擠軋過程的金屬流動,但送進角過大會造成管坯金屬材料過度變形, 降低 管坯的表面質(zhì)量。
當軋輥公轉(zhuǎn)速度過大時, 軋輥和 管坯接觸區(qū)的相對速度矢量過大使得材料塑性變形 能力降低, 尺寸精度降
低。 管坯前進速度過小會導(dǎo) 致管坯在單位時間內(nèi)受到軋輥更多軋制, 管坯成形 質(zhì)量變差, 管坯前進速度
過大會使管坯壁厚不均勻 和擴徑量增大。 (3) 對TA2鈦管擠軋成形的正交模擬試驗結(jié)果進行管坯尺寸精
度分析, 優(yōu)化得到一組工藝參數(shù)W= 150r·min-1, V = 5mm·s-1, α = 6°。 通
過優(yōu)化 的工藝參數(shù)進行擠軋試驗, 擠軋得到的TA2鈦管外 徑偏差為 0.12mm, 內(nèi)徑偏差為 0.06mm, 壁
厚偏 差為 0.05mm, 管坯表面質(zhì)量良好。
參考文獻:
[1]楊彪, 王平, 龔云柏, 等.油氣行業(yè)
用鈦合金油井管生產(chǎn)與 研究應(yīng)用進展 [J].材料熱處理學(xué)報, 2021, 42 ( 9): 12- 21.
YANGBiao, WANGPing, GONGYunbai,
etal.Progressinmanufacturingandapplicationresearchoftitaniumalloyoilcountrytubulargoodsforpetr
oleumandnaturalgasindustry [J].TransactionsofMaterialsandHeatTreatment, 2021, 42(9):12-
21.
[2] 孫靜娜, 向文杰, 徐森.TC4 鈦合金
板軋制換熱系數(shù)實驗研 究 [J].塑性工程學(xué)報, 2022, 29 (3): 59-65.
SUNJingna, XIANGWenjie,
XUSen.ResearchonheattransfercoefficientinrollingforTC4titaniumalloyplate [
J].JournalofPlasticityEngineering, 2022, 29(3):59-65.
[3] 張關(guān)梅, 黃海廣, 張浩澤, 等.軋制
溫度對 TA31 鈦合金熱 軋板材組織與性能的影響 [ J].塑性工程學(xué)報, 2022, 29 (11): 224-232.
ZHANGGuanmei, HUANGHaiguang, ZHANGHaoze,
etal.EffectofrollingtemperatureonmicrostructureandpropertiesofTA31titaniumalloyhotrolledplate
[J].JournalofPlasticityEngineering, 2022, 29(11):224-232.
[4] 劉新華, 林一良, 付華棟, 等.毛細
銅/ 鈦復(fù)合管材的游動 芯頭拉拔制備及組織性能 [ J].工程科學(xué)學(xué)報, 2017, 39 (3): 417-
425.
LIUXinhua, LINYiliang, FUHuadong,
etal.Preparationofthecapillarycopper/ titaniumcompositepipebyfloating-
plugdrawingprocessinganditsmicrostructureandproperties [ J].ChineseJournalofEngineering, 2017,
39(3):417-425.
[5] 羅登超, 王云, 李維.不同工藝制備
TA15 鈦合金管材 [ J].鍛壓技術(shù), 2022, 47 (8): 118-122.
LUODengchao, WANGYun,
LIWei.ManufactureofTA15titaniumalloypipesbydifferentprocesses [
J].Forging&StampingTechnology, 2022, 47 (8):118-122.[6] XUWC, SHANDB, WANGZL,
etal.EffectofspinningdeformationonmicrostructureevolutionandmechanicalpropertyofTA15titaniumal
loy [J].TransactionsofNonferrousMetalsSocietyofChina, 2007, 17 (6):1205-1211.
[7]尹業(yè)宏, 黃旺, 鄧緒水, 等.基于
Deform-3D 的冷軋鈦管有 限元分析 [J].鍛壓技術(shù), 2014, 39 (9): 122-126.YINYehong, HUANGWang,
DENGXushui, etal.Finiteelementanalysisofcold-rolledtitaniumtubebasedonDeform-3D
[J].Forging&StampingTechnology, 2014, 39 ( 9 ):122 - 126.[8]周大地, 曾衛(wèi)東, 徐建偉.斜軋穿
孔法制備Ti80合金無縫管 工藝 分 析 [ J].稀 有 金 屬 材 料 與 工 程, 2020, 49 ( 3 ): 1045-
1050.
ZHOUDadi, ZENGWeidong,
XUJianwei.RotarypiercingtechniqueofTi80titaniumalloyseamlesstube
[J].RareMetalMaterialsandEngineering, 2020, 49 (3):1045-1050.
[9]ZHANGZ, LIUD, YANGYH,
etal.Explorativestudyofrotarytubepiercingprocessforproducingtitaniumalloythick-
walledtubeswithbi-modalmicrostructure [J].ArchivesofCivilandMechanicalEngineering, 2018, 18
(4):1451-1463.[10] 謝林均, 朱栓平.擠壓速度對TA16鈦合金管坯熱擠壓成型的 影響 [J].世界有色金
屬, 2021, (19): 132-133.
XIELinjun,
HUShuanping.EffectofextrusionspeedonhotextrusionformingofTA16titaniumalloytubeblank [
J].WorldNonferrousMetals, 2021, (19):132-133.
[11] DAMODARAND,
SHIVPURIR.Predictionandcontrolofpartdistortionduringthehotextrusionoftitaniumalloys [
J].JournalofMaterialsProcessingTechnology, 2004, 150 (1 / 2):70-75.
[12] EBRAHIMIM, TABEIKH, NASERIR,
etal.Effectofflowformingparametersonsurfacequality,
geometricalprecisionandmechanicalpropertiesoftitaniumtube
[J].ProceedingsoftheInstitutionofMechanicalEngineers,
PartE.JournalofProcessMechanicalEngineering, 2018, 232 (6):702-708.
[13]于輝, 李偉, 曾林, 等.鈦合金連鑄
管坯的擠軋一體化成形 方法: 中國, CN110883124B [P].2020-08-28.YUHui, LIWei, ZENGLin,
etal.Integratedextrusion-
rollingformingmethodfortitaniumalloycontinuouscastingtubebillets:China, CN110883124B [P].2020
-08-28.
[14]于輝, 岳恒全, 陳恩平, 等.小型管
坯旋轉(zhuǎn)擠軋成形裝置及 其擠軋成形方法: 中國, CN115026132A [P].2022-09-09.
YUHui, YUEHengquan, CHENEnping,
etal.Smalltubeblankrotaryextrusion-rollingformingdeviceanditsextrusion-
rollingformingmethod:China, CN115026132A [P].2022-09-09.[15]尚筱迪.工藝純鈦TA2熱壓縮變形行
為及微觀組織演變[D].西安: 西安建筑科技大學(xué), 2019.
SHANGXiaodi.HotdeformationbehaviorandmicrostructureevolutionofTA2 [D].Xi′an:Xi
′anUniversityofArchitectureandTechnology, 2019.
[16]陸燕玲.TA2、 TC4 熱軋工藝制度研
究 [D].上海: 上海交 通大學(xué), 2009.LUYanling.ResearchonthehotrollingprocesssystemofTA2andTC4
[D].Shanghai:ShanghaiJiaoTongUniversity, 2009.
[17]夏琴香, 吳競飛, 程秀全, 等.旋輪
結(jié)構(gòu)對高強鋼筒形件流 動旋壓成形影響規(guī)律研究 [ J].模具技術(shù), 2017, (2): 1- 5.
XIAQinxiang, WUJingfei,
CHENGXiuquan,
etal.Researchontheinfluenceofrollerstructureonformingqualityofhighstrengthsteelduringflowspinn
ingforming [ J].DieandMouldTechnology, 2017, (2): 1-5.
[18] 平欣, 平鵬.圓度、 同軸度和圓柱
度誤差的最小二乘評定法[J].實用測試技術(shù), 1997, (2): 44-45, 26.
PINGXin,
PINGPeng.Leastsquaresevaluationmethodforroundness, coaxialityandcylindricityerrors
[J].ChinaMeasurement&Test, 1997, (2):44-45, 26.
[19] GB/ T3624—2010, 鈦及鈦合金無縫
管 [S].GB/ T3624—2010, Titaniumandtitaniumalloyseamlesstubes [S].
相關(guān)鏈接