引言
隨著石油化工行業(yè)不斷發(fā)展,化工設(shè)備的耐腐蝕性能和承壓能力需要滿足越來越高的要求。鈦材是一種常用的耐腐蝕材料,尤其對中性、氧化性、弱還原性介質(zhì)有著較好的耐腐蝕性,而鈦-鋼復(fù)合板兼具鈦材料優(yōu)秀的耐腐蝕性能和低合金鋼的力學(xué)性能,既能降低材料成本,又能保證設(shè)備本體的強(qiáng)度和剛度,因此鈦-鋼復(fù)合板已成為化工設(shè)備中最常用的材料。
由于鈦材不能與鋼材直接焊接,鈦一鋼復(fù)合板設(shè)備在設(shè)計、制造、檢驗等方面,都與常規(guī)的鋼制壓力容器有較大的區(qū)別。本文以鈦一鋼復(fù)合板作為主體材料的U形管換熱器為例,介紹了管箱分程隔板和鈦U型管束在制造、組裝過程中,與筒體內(nèi)部鈦貼條、鈦蓋板產(chǎn)生干涉,使得殼體內(nèi)部鈦貼條、鈦蓋板焊縫被破壞的問題。在不影響設(shè)備換熱效率和結(jié)構(gòu)強(qiáng)度的前提下,提出了管束制造以及組裝的相應(yīng)解決方案,保證分程隔板和U型管束順利安裝。
1、設(shè)備基本參數(shù)及結(jié)構(gòu)特點
該U形管換熱器主要設(shè)計參數(shù)可見表1。
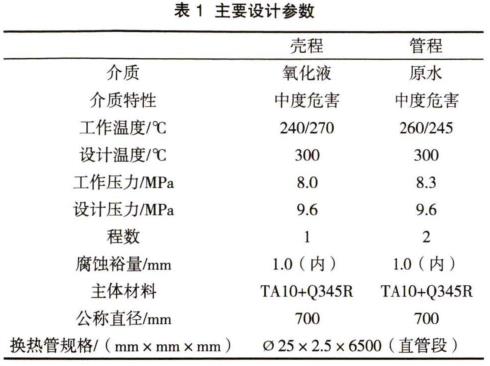
1.1 材料選用
設(shè)備管、殼程介質(zhì)均具有弱酸性,且設(shè)計壓力和設(shè)計溫度較高,筒體和封頭材料選用TA10+Q345R(正火合板,設(shè)備法蘭材料為16MnⅢ鍛件襯TA10板,管板采用純TA10鍛件,拉桿、定距管、折流板材料均采用TA10,管箱和殼程側(cè)墊片采用柔性石墨復(fù)合墊,緊固件材料采用35CrMoA。
1.2 結(jié)構(gòu)特點
TA10板作為設(shè)備耐腐蝕層,不參與強(qiáng)度計算,設(shè)備主要承壓是基層鋼板。根據(jù)GB/T150.3一2011K壓力容器第3部分:設(shè)計》中內(nèi)壓圓筒和封頭的計算公式,該設(shè)備經(jīng)過計算并圓整取筒體基層厚度為28mm,封頭基層厚度為26mm(成形后),覆層采用厚度為3mm的TA10板作為耐腐蝕層,鈦-鋼復(fù)合板按標(biāo)準(zhǔn)NB/T47002.3—2019《壓力容器復(fù)合板第3部分:鈦一鋼復(fù)合板》標(biāo)準(zhǔn)中B1級的規(guī)定,鈦-鋼復(fù)合板焊接接頭按HG/T20583—2020附錄E(規(guī)范性)執(zhí)行,基層焊接完畢后焊縫內(nèi)側(cè)設(shè)置焊接鈦墊板和貼條,并在貼條拼接處設(shè)置蓋板(詳見圖1);環(huán)向焊接接頭鈦貼條端部和縱、環(huán)焊接接頭連接處的T形接頭采用鈦制蓋板覆蓋(詳見圖2);該設(shè)備焊接接頭用鈦墊板、貼條及蓋板厚度均為3mm,因此縱環(huán)焊縫處的鈦貼條較設(shè)備內(nèi)徑凸起為3mm,蓋板凸起為6mm。
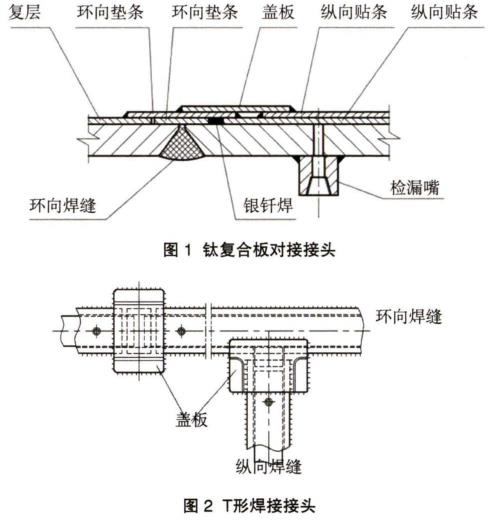
2、 分程隔板設(shè)計
2.1 厚度計算
根據(jù)GB/T1512014《熱交換器》,分程隔板厚度δ計算公式為:
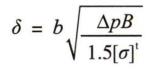
式中:
b一一隔板長度;
B一一尺寸系數(shù);
△p一一隔板兩側(cè)壓力差;
[σ]t一一隔板材料設(shè)計溫度下的許用應(yīng)力。
分程隔板兩側(cè)均考慮1mm腐蝕,通過計算并圓整后該隔板厚度取16mm。分程隔板與管箱采用焊接連接,在管箱法蘭密封面處分程隔板端部厚度應(yīng)比管板上對應(yīng)的隔板槽寬度小2mm便于組裝。當(dāng)分程隔板厚度根據(jù)強(qiáng)度計算需要比較厚,且管板分程處隔板槽尺寸限制時,對分程隔板端部結(jié)構(gòu)進(jìn)行削?。ㄔ斠妶D3),并在分程隔板上設(shè)置φ6mm的排凈孔,同時分程隔板端部需與管箱設(shè)備法蘭的密封面進(jìn)行二次加工,保證隔板端部與管箱法蘭端部密封面粗糙度一致。
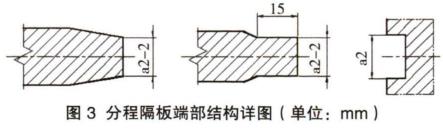
2.2 結(jié)構(gòu)設(shè)計
鈦復(fù)合板設(shè)備的分程隔板與管箱殼體覆層焊接,管箱筒體環(huán)向焊接接頭處鈦貼條較管箱內(nèi)壁凸出3mm,分程隔板與環(huán)向鈦貼條干涉無法安裝,如果直接減小分程隔板的寬度避開鈦貼條,將會造成分程隔板與管箱復(fù)層焊接間隙太大無法保證焊接質(zhì)量。
本文提出的方案是將分程隔板在環(huán)向焊接接頭處進(jìn)行開槽處理,避開環(huán)向鈦貼條(詳見圖4),管箱環(huán)向焊接接頭組焊完畢后,先組裝管箱內(nèi)側(cè)的鈦墊板,保證鈦墊板組裝后與復(fù)合板覆層面高度一致,然后組裝分程隔板,分程隔板放人管箱后先不進(jìn)行焊接,將環(huán)向鈦貼條裝人管箱并從分程隔板開槽穿過并完成鈦貼條角焊縫的焊接,最后再調(diào)整隔板方位至圖紙要求位置,并焊接分程隔板與管箱的連接焊縫。
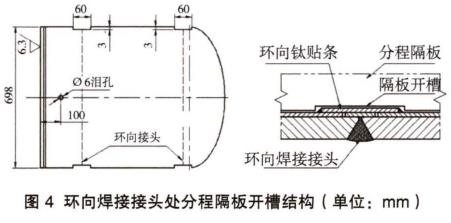
3、 裝配管束
U形管換熱器管束可拆卸,管束和殼程清洗較為方便,鈦-鋼復(fù)合板對接接頭內(nèi)部鈦貼條和蓋板凸起,安裝或拆卸管束時貼條和蓋板與折流板干涉,甚至?xí)斐少N條和蓋板焊縫被破壞。因此針對U形管束安裝問題提出解決方案。
3.1 減小折流板外徑
常規(guī)換熱設(shè)備的折流板外徑及允許偏差按GB/T151一2014標(biāo)準(zhǔn)中表6-20確定,由于鈦-鋼復(fù)合板對接接頭內(nèi)部貼條貫穿筒體封頭所有的縱、環(huán)焊縫,折流板外徑比GB/T151一2014標(biāo)準(zhǔn)要求的尺寸減小6mm(2個環(huán)縫貼條厚度),保證折流板安裝時不與筒體上對接接頭貼條干涉。
3.2 設(shè)置防短路墊環(huán)
折流板作用是支撐換熱管和提高殼程流體的流速,增加動程度,并使殼程流體垂直沖刷管束,以改善傳熱效果,增大殼程流體的傳熱系數(shù),同時減少結(jié)垢,提高換熱效率。折流板直徑一般略小于設(shè)備直徑,便于管束裝配,如果折流板外徑在標(biāo)準(zhǔn)規(guī)定尺寸的基礎(chǔ)上再減小6mm,將會造成折流板與殼體間的間隙過大,有害流路就會增大,部分流體短路,換熱效率被削弱。為了解決這個問題,本設(shè)備的設(shè)計方案為:在殼程筒體內(nèi)部設(shè)置鈦墊環(huán),焊接在殼程筒體內(nèi)壁,墊環(huán)厚度為3mm,墊環(huán)放置在管束穿人殼程筒體內(nèi)部后,折流板所在位置。在每個折流板位置設(shè)置一圈鈦墊環(huán)(詳見圖5),確保折流板與筒體間的間隙滿足標(biāo)準(zhǔn)要求,從而保證換熱器的換熱效率。
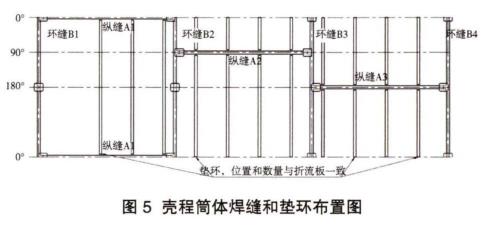
最后在環(huán)向焊接接頭鈦貼條端部和縱、環(huán)焊接接頭連接處的T形接頭所在方位,折流板上開矩形槽,保證折流板不與鈦蓋板干涉。
3.3 支撐導(dǎo)軌和滑道
采用支撐導(dǎo)軌結(jié)構(gòu)可以固定管束安裝方位,起到限位作用,避免管束安裝過程中發(fā)生角度偏轉(zhuǎn)從而造成折流板與蓋板發(fā)生碰撞。折流板與滑道配合開槽并設(shè)置滑桿(詳見圖6),保證管束能順利穿入筒體。
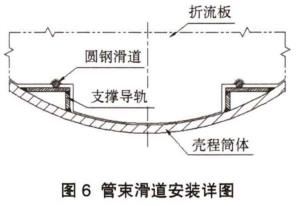
為了保證管束在安裝過程中順滑平穩(wěn),支撐導(dǎo)軌與圓鋼滑道配合面需保持水平,導(dǎo)軌與殼程筒體環(huán)縫貼條干涉處應(yīng)開槽錯開,導(dǎo)軌上筋板與滑道連接段保持連續(xù),下筋板斷開(詳見圖7)。
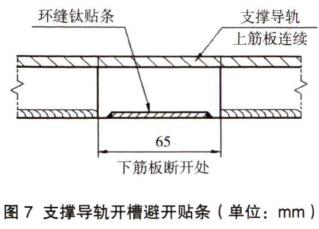
3.4 導(dǎo)軌和滑道另一種設(shè)計方案
支撐導(dǎo)軌和圓鋼滑道配合是一種常用的管束安裝方法,該方法穩(wěn)定性好,易檢修;同時也可采用滾輪式滑道,當(dāng)介質(zhì)為潔凈流體時也具有很高的穩(wěn)定性,但對于殼程介質(zhì)黏度較大或介質(zhì)含有固體雜質(zhì)易結(jié)垢等場合,滾輪可能會出現(xiàn)滾輪卡死、或阻力過大難以拆卸的情況。支撐導(dǎo)軌結(jié)構(gòu)也可作為滾輪式導(dǎo)軌結(jié)構(gòu)的一種補(bǔ)充方案,并且支撐導(dǎo)軌完全避開了管束直接在復(fù)合板筒體耐腐蝕層表面直接滑動,減少了耐腐蝕層的磨損,對于大型U型管換熱器也同樣適用。
4、結(jié)語
U形管換熱器管、殼程筒體為鈦-鋼復(fù)合板時,其在縱、環(huán)對接焊縫處存在凸起的鈦貼條和鈦蓋板,進(jìn)而導(dǎo)致設(shè)備內(nèi)件組裝無法按常規(guī)設(shè)計進(jìn)行,而且設(shè)計階段容易被忽略,導(dǎo)致設(shè)備組裝過程時強(qiáng)行操作,甚至造成鈦蓋板和貼條被破壞。故本文U形管換熱器在結(jié)構(gòu)設(shè)計階段提出了關(guān)于分程隔板相應(yīng)結(jié)構(gòu)修改和組裝順序,及管束組裝時折流板處的結(jié)構(gòu)特殊處理,既保證了換熱器正常使用和換熱效率,又能滿足設(shè)備結(jié)構(gòu)強(qiáng)度和穩(wěn)定性。
相關(guān)鏈接