近年來,由于國家對(duì)于環(huán)保的高度重視,工業(yè)生產(chǎn)中高濃度有機(jī)廢水不可隨意排放,可以通過一種新型水處理技術(shù)—催化濕式氧化法來進(jìn)行綜合治理,該法是指在高溫、高壓下,以富氧氣體或氧氣為氧化劑,利用催化劑的催化作用,使廢水中的有機(jī)物及含S、N等氧化成CO2,N2,SO2,H2O,達(dá)到凈化水的目的。本文設(shè)計(jì)討論的是其工藝裝置中的1臺(tái)一級(jí)U形管換熱器,設(shè)備內(nèi)徑為ID600換熱器參數(shù)如下:
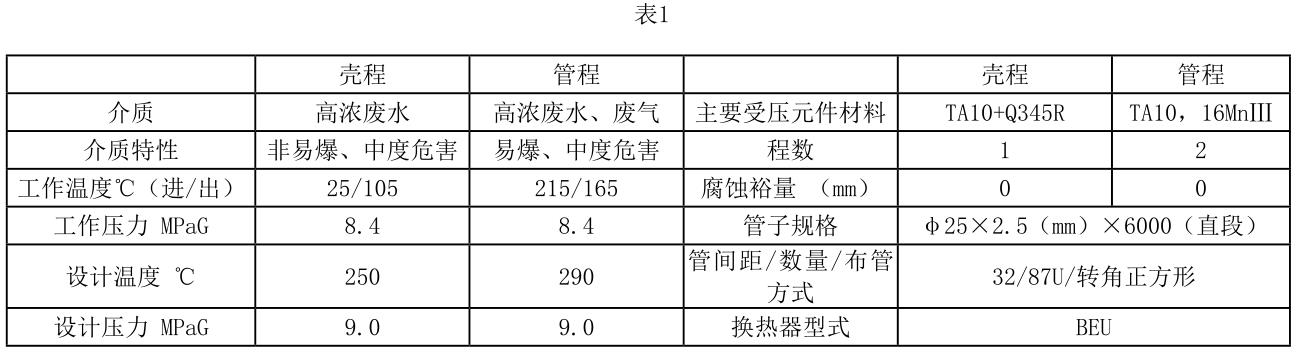
1、 選用材料
殼程殼體采用TA10+Q345R爆炸復(fù)合板,其中TA10材料在GB/T 3621-2007 《鈦及鈦合金板材》中分為A、B兩類,B類板材的常溫抗拉強(qiáng)度、屈服強(qiáng)度比A類小,更容易進(jìn)行爆炸復(fù)合,所以用于爆炸復(fù)合板時(shí),需注明采用B類,否則正常供貨按A類,爆炸復(fù)合板不合格率會(huì)大大提高。
殼程其他材料如:拉桿、定距管、折流板均采用TA10。管程采用平蓋封頭襯鈦結(jié)構(gòu),管板、換熱管TA10分別滿足GB/T16598-2013《鈦及鈦合金餅和環(huán)》、GB/T3625-2007《換熱器及冷凝器用鈦及鈦合金管》。連接的緊固件為35CrMoA,螺母為30CrMoA;墊片為帶覆蓋層的金屬齒形組合墊,齒形金屬環(huán)材料為TA10,覆層材料為柔性石墨墊片m=3.5,y=45MPa。
2、 強(qiáng)度計(jì)算
(1)鈦?zhàn)鳛槟透g層厚度常為2~4mm,在復(fù)合板筒體中一般不參與強(qiáng)度計(jì)算,設(shè)備的承壓主要是基層殼體。
(2)爆炸復(fù)合管板計(jì)算。由于我們通常采用SW6計(jì)算軟件,復(fù)層不參與計(jì)算,軟件輸入的是管板基層材料,對(duì)于換熱管與管板連接采用焊接連接的換熱管的許用拉脫力,應(yīng)為復(fù)層與換熱管材料在設(shè)計(jì)溫度下兩者中小值的0.5倍,而軟件判斷的是參與計(jì)算的基層與換熱管材料在設(shè)計(jì)溫度下兩者中小值的0.5倍,這需要特別注意。而本次設(shè)計(jì)的結(jié)構(gòu)為BEU形管熱交換器,管板采用的是純TA10材料與換熱管同材質(zhì),不存在拉脫力判斷錯(cuò)誤問題。
(3)對(duì)于接管中的鈦襯管,如果設(shè)備內(nèi)有負(fù)壓需要考慮襯管的外壓失穩(wěn)計(jì)算,本臺(tái)設(shè)備無外壓,可以忽略。
3 、設(shè)計(jì)結(jié)構(gòu)
(1)管箱設(shè)計(jì)
管程壓力及溫度較高,為了節(jié)約成本,管箱采用襯鈦結(jié)構(gòu)(圖1)。其中襯鈦部分由底板及鈦環(huán)組成,焊接采用全焊透結(jié)構(gòu),圖中t1的最小計(jì)算厚度需要滿足接管上的外載荷及內(nèi)部壓力的強(qiáng)度要求。碳鋼部分是承受壓力的主體,采用碗形鍛件。
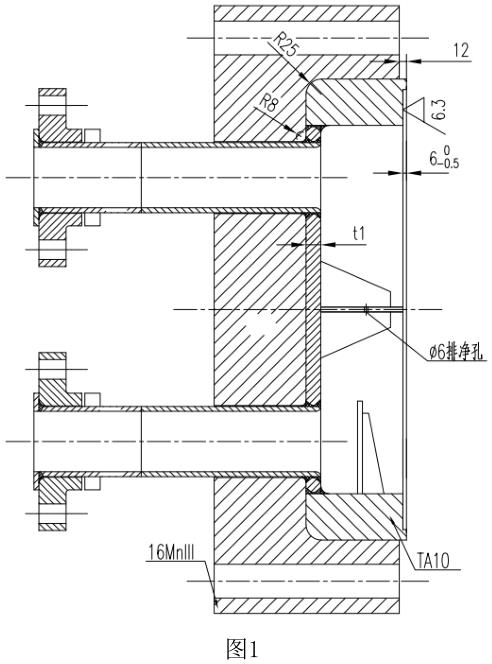
管箱深度不小于進(jìn)口接管內(nèi)徑的1/3,為了減少進(jìn)口接管對(duì)換熱管管頭的沖刷,增加了防沖擋板。管箱分程隔板采用了帶加強(qiáng)筋結(jié)構(gòu)進(jìn)行優(yōu)化。
(2)管束
①換熱管與管板連接結(jié)構(gòu)
鈦材的強(qiáng)度和彈性模量隨著溫度的升高而有較大幅度的降低,且在常溫下有蠕變傾向,使換熱管和管板的脹接殘余應(yīng)力松弛,易引起泄漏,所以一般不推薦使用強(qiáng)度脹接。鈦換熱管一般采用焊接連接,焊接比強(qiáng)度脹接更能保證強(qiáng)度及密封性能。但管板和換熱管之間總有縫隙存在,這樣最容易產(chǎn)生縫隙腐蝕。為此采用貼脹加焊接結(jié)合的連接方式效果實(shí)踐證明比較好,既提高了接頭的抗疲勞性能,又可消除應(yīng)力腐蝕破裂和縫隙腐蝕,本設(shè)計(jì)采用的是此結(jié)構(gòu)(圖2)。
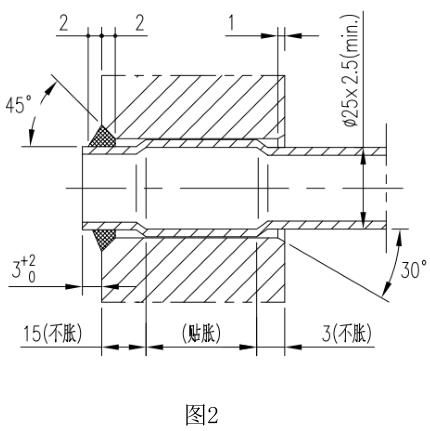
鈦的導(dǎo)熱系數(shù)小,是碳素鋼的1/4,銅的1/25,一般選用的換熱管為薄壁管。換熱管與管板焊接時(shí)會(huì)產(chǎn)生較大的熱應(yīng)力,管端焊縫還需要承載內(nèi)壓產(chǎn)生的拉脫力,加上進(jìn)口管的高壓氣流吹掃,管端焊縫經(jīng)過沖刷,表面無損檢測(cè)無法發(fā)現(xiàn)的微觀裂紋,就會(huì)暴露出來,大大降低連接強(qiáng)度,可能導(dǎo)致焊縫破壞。我們通常的做法是管端不熔,管頭伸出管板面至少3mm,在焊縫破壞之前,讓管頭承受沖擊,以提高設(shè)備的使用壽命。
鈦材的屈強(qiáng)比較高,斷面收縮率較低,延伸性差,不易產(chǎn)生較大變形,為防止脹管開裂,管板開孔直徑應(yīng)盡量采用小的孔徑,小的偏差,需要滿足GB/T 151-2014表6-15的要求。
②U形管設(shè)計(jì)
U形管的最小彎曲半徑為2d(d為換熱管外徑),前期與換熱管彎制廠家溝通確認(rèn)無問題后,最終確定;因鈦管一般較薄,JB/T4745-2002中10.2.6.2條規(guī)定彎管外圓弧處的壁厚減薄量不應(yīng)超過17%的名義厚度。U形管存在一定量的回彈性,管束設(shè)計(jì)時(shí),最后一塊折流板面與U形管直管段切線距離最少保證30mm以上的距離。彎制成形后的U形管一般不做熱處理。
③折流板
對(duì)于鈦制換熱器來說,折流板的設(shè)計(jì)需引起重視。首先由于鈦材的摩擦系數(shù)大,易產(chǎn)生粘連性等特性。當(dāng)折流板是鈦材時(shí),設(shè)計(jì)時(shí)應(yīng)慎重考慮與鈦材換熱管間的相互摩擦作用。通過工藝計(jì)算,優(yōu)化設(shè)備結(jié)構(gòu),減少管束振動(dòng),從而消除摩擦。折流板孔的兩端面應(yīng)嚴(yán)格進(jìn)行倒角,不允許有銳角出現(xiàn),否則換熱管很容易被穿管時(shí)劃傷、使用過程中磨損破裂。另外要注意孔徑的大小,不能太小但也不是大了就好,因?yàn)樘螅ㄈ玳g隙0.4mm)時(shí)會(huì)有高速液流沖刷管子,使管子發(fā)生沖刷腐蝕,折流板孔徑大小需要按GB/T 151-2014表6-28設(shè)計(jì)。
(3)殼程結(jié)構(gòu)設(shè)計(jì)
①殼程筒體A、B類焊縫對(duì)接結(jié)構(gòu),殼程的最高工作溫度為105℃,工作壓力為8.4MPa,且換熱管束需要抽插,最終我們采用了如圖3的平貼條結(jié)構(gòu)(圖3)。優(yōu)點(diǎn)是耐壓、便于制造、安裝及使用。缺點(diǎn)是耐高溫性能不好,不過經(jīng)過我們多年經(jīng)驗(yàn)積累發(fā)現(xiàn)并經(jīng)計(jì)算得知,如果設(shè)備內(nèi)介質(zhì)的工作溫度低于220℃,采用平貼條結(jié)構(gòu)可以使用。
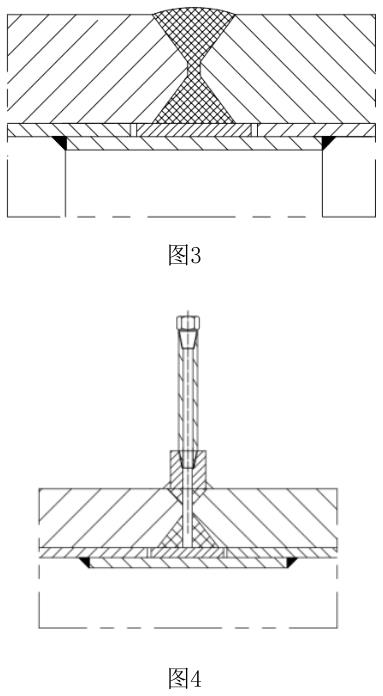
在焊接基層A、B類對(duì)接接頭時(shí),先采用機(jī)械方法剔除焊接接頭兩側(cè)各15mm的鈦復(fù)層,防止基層金屬熔焊到鈦復(fù)層中,同時(shí)也可以防止鈦復(fù)層因溫度過高發(fā)生氧化。基層焊接完畢,將容器內(nèi)側(cè)的基層焊縫磨平并經(jīng)無損檢測(cè)合格后,放置一塊鈦墊條,鈦墊條與鈦復(fù)層間點(diǎn)焊固定。然后在鈦墊板上覆蓋一層鈦貼條,鈦貼條和鈦覆層之間進(jìn)行角焊縫連續(xù)焊接。
②T形接頭。
在焊接墊條前,先鉆墊條腔檢漏孔φ6,只鉆通基層(圖4)。墊條腔檢漏孔的設(shè)置在筒體縱環(huán)焊縫上,由于本臺(tái)設(shè)備直徑不大在縱縫兩端進(jìn)行隔腔,縱環(huán)丁字焊縫處可以不分腔。墊條與復(fù)層點(diǎn)焊固定,分腔處附近的墊條與墊條、墊條與復(fù)層需要焊接。銀釬焊后的區(qū)域墊上δ3×10×30大小的鈦板,分腔處銀釬焊封焊一圈,與以往結(jié)構(gòu)相比銀釬焊面積相對(duì)增加,而且相當(dāng)于雙層隔斷,效果更好。然后組裝并焊接相關(guān)的縱焊縫和環(huán)焊縫貼條,注意環(huán)縫貼條與縱縫連接處留25mm不焊,使蓋板與環(huán)縫貼條共腔,不留死區(qū)連續(xù)焊。貼條焊接完成,蓋板組焊前,先進(jìn)行貼條腔檢漏。T形接頭的組裝順序見圖5。
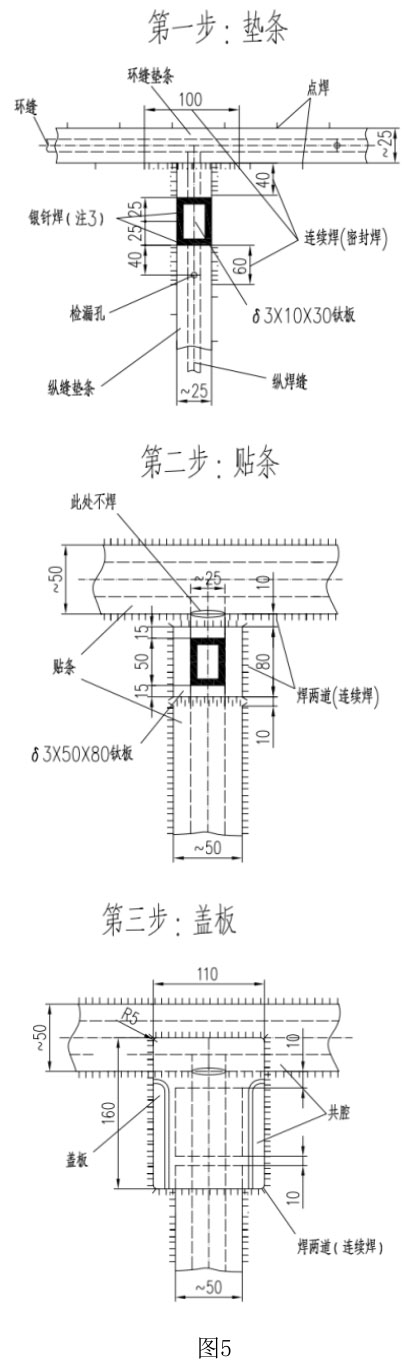
③檢漏孔
在鈦制復(fù)合板設(shè)備的縱、環(huán)焊縫T形接頭處、法蘭接管上等外接件與殼體連接的轉(zhuǎn)角處應(yīng)設(shè)置檢漏孔,確保每個(gè)腔至少有兩個(gè)檢漏孔,每個(gè)腔的長度不大于8m。其檢漏孔的作用有:(1)在焊接時(shí),使所有處于高溫焊接部位的鈦材得到氬氣的有效保護(hù),防止氧化。(2)用于檢驗(yàn)制造過程中貼條與復(fù)層處的焊縫是否存在泄漏。(3)用于檢驗(yàn)設(shè)備在役使用期間是否產(chǎn)生漏點(diǎn),提前預(yù)警。
④接管與殼體焊接結(jié)構(gòu)
對(duì)于襯鈦設(shè)備的管口,一般法蘭采用WN或LWN,襯管外徑與接管內(nèi)徑單邊間隙小于等于0.5(圖6)。在接管焊接接頭與殼體復(fù)合處,剔出超過焊縫坡口5mm,用鈦墊條實(shí)配填充完整并點(diǎn)焊固定,保證鈦墊條的表面與覆層鈦材的表面齊平。接管根部附近的鈦襯里應(yīng)搭接在殼體的復(fù)層鈦之上,搭接長度一般為80~100mm。在基層上的低點(diǎn)及接管處高點(diǎn)分別鉆兩個(gè)φ6的檢漏孔。鋼管的內(nèi)表面需處理干凈光潔后,與鈦襯里預(yù)組裝,直到緊貼為止,方可進(jìn)行接管與殼體的焊接。為了減少襯鈦接管與殼體連接處焊接接頭的最大應(yīng)力,保證交接處有足夠的撓性,設(shè)計(jì)時(shí)應(yīng)加以重視,必要時(shí)需要加以核算。本設(shè)備因溫度及壓力較高,采用的是帶翻邊結(jié)構(gòu)(圖7),其中R的選取根據(jù)接管公稱直徑來定(DN≤40,R=12;DN≤150,R=19;DN≤500,R=25;DN>500,R=32)。
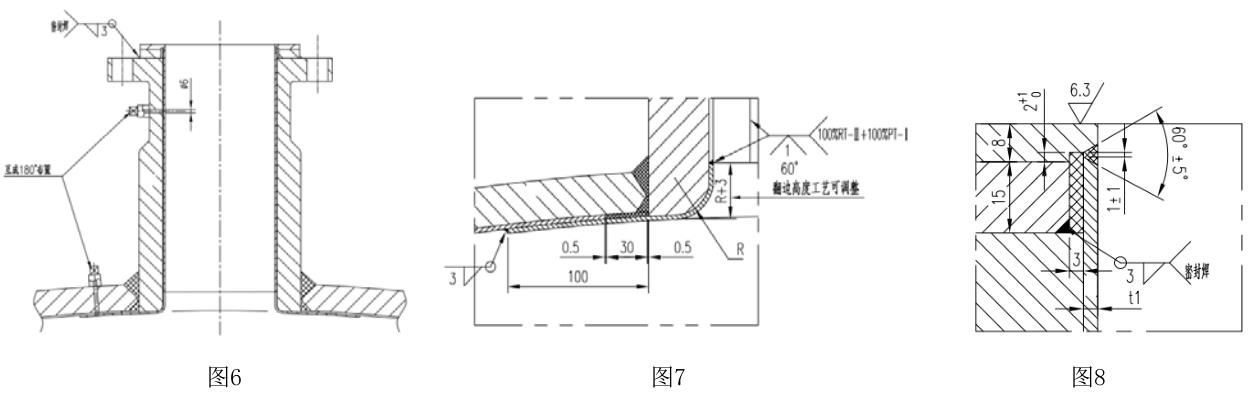
⑤法蘭密封面連接結(jié)構(gòu)
接管法蘭密封面通常采用碳鋼法蘭襯鈦的方法。碳鋼法蘭承受螺栓緊固載荷及相連管道載荷,鈦材層僅作為耐腐蝕的密封面。在鈦層非密封面上均勻設(shè)置一定數(shù)量的鈦制沉頭螺釘與碳鋼法蘭連接,螺釘所在的圓為法蘭螺栓圓,鈦制沉頭螺釘與鈦材之間用氬弧焊密封之后進(jìn)行機(jī)械加工密封面,滿足圖紙密封面的機(jī)加工要求,此類結(jié)構(gòu)主要用于設(shè)備工作壓力、溫度及使用工況要求不高的場(chǎng)合。因本臺(tái)設(shè)備工作壓力大、溫度高及工況復(fù)雜,我們采用了爆炸復(fù)合板密封面結(jié)構(gòu)(圖8)。設(shè)備法蘭的密封面結(jié)構(gòu)采用與接管法蘭密封面同樣的結(jié)構(gòu),而法蘭與筒體連接結(jié)構(gòu)(圖9)。
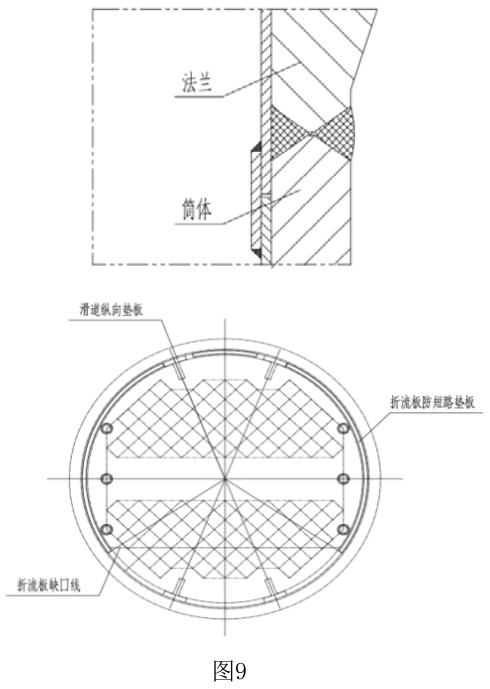
⑥折流板與筒體間防短路設(shè)計(jì)
殼程筒體由于帶有縱環(huán)焊縫的貼條及T形蓋板,因此折流板的外徑比GB/T 151規(guī)定的外徑基礎(chǔ)上扣除2倍的貼條厚度。折流板缺口處不焊接防短路墊板(圖10)。其中抽插管束中于設(shè)備內(nèi)部殼體鈦蓋板相干涉的折流板修割缺口。
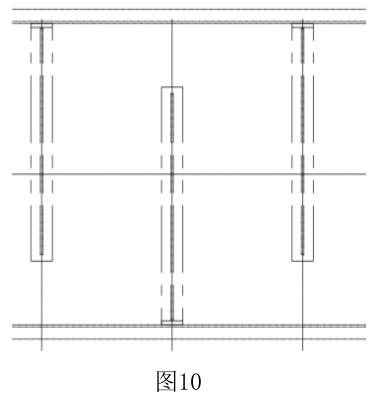
4、 其他要求 熱氣循環(huán)試驗(yàn)
由于鈦的線膨脹系數(shù)小于碳鋼和低碳鋼,而且鈦鋼復(fù)合板設(shè)備內(nèi)鈦的焊縫較多,使鈦的復(fù)層焊縫在加熱時(shí)始終處于受拉伸應(yīng)力狀態(tài)。另外鈦在焊接過程中因材料本身及焊接方面的原因也會(huì)存在焊縫缺陷,極易使鈦焊縫產(chǎn)生開裂,從而造成滲漏。因此對(duì)比較重要的核心復(fù)層焊縫設(shè)備進(jìn)行熱氣循環(huán)試驗(yàn),防止設(shè)備在使用過程中出現(xiàn)不可預(yù)測(cè)質(zhì)量事故。根據(jù)我公司工藝部門內(nèi)部制定的熱氣循環(huán)試驗(yàn)操作程序,以設(shè)計(jì)壓力、設(shè)計(jì)溫度、氮?dú)鉃楣ぷ鹘橘|(zhì)進(jìn)行試驗(yàn),試驗(yàn)結(jié)果一次合格。
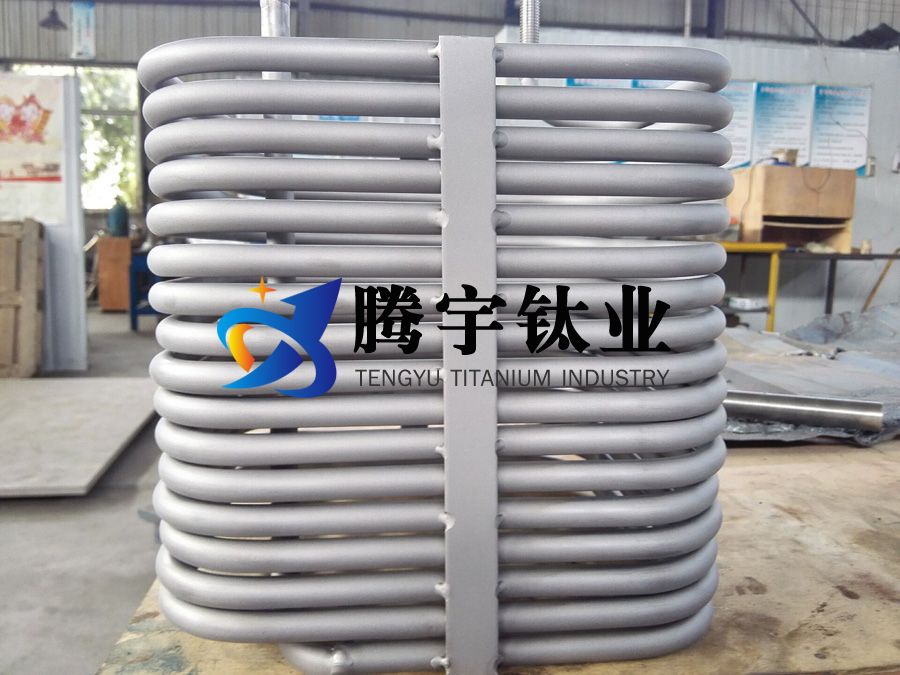
5、 結(jié)語
因鈦材的自身特性,決定了其有很多技術(shù)要點(diǎn)值得注意。設(shè)計(jì)人員應(yīng)充分結(jié)合實(shí)際制造中的要求,在材料、設(shè)計(jì)、制造及過程檢測(cè)等方面進(jìn)行綜合考慮,確保鈦制設(shè)備在設(shè)計(jì)使用年限內(nèi)安全可靠。本文根據(jù)筆者幾年前審核的一臺(tái)鈦制U形管換熱設(shè)備的實(shí)踐經(jīng)驗(yàn),提出了一些設(shè)計(jì)中應(yīng)注意的事項(xiàng),供同行討論。目前此設(shè)備在役使用狀況良好。
參考文獻(xiàn)
[1] JB/T 4745-2002,鈦制焊接容器[S].
[2] GB /T 151-2014,熱交換器[S].
[3] 黃嘉琥,應(yīng)道宴等編. 鈦制化工設(shè)備[M].北京:化學(xué)工業(yè)出版社,2002.
[4] NB/T 47002.1~4-2009,壓力容器用爆炸焊接復(fù)合板[S].
相關(guān)鏈接