環(huán)氧丙烷裝置氯醇液換熱器的工藝流程如下:
鈦塔出來得氯丙醇液(大量的水、3%-3.8%的氯丙醇、1.5%-1.75鹽酸)從60℃預(yù)熱到72℃左右。根據(jù)設(shè)計(jì)選用了固定管板式鈦換熱器,鈦材的最大優(yōu)點(diǎn)是耐蝕性能好,它的耐蝕性遠(yuǎn)遠(yuǎn)超過不銹鋼。鈦在自然條件下或含氧氣氛中,其表面會(huì)形成一層致密的氧化膜,該膜能抵抗比如鈦與濕氯、氯化物等多種化學(xué)介質(zhì),氧化性、中性介質(zhì),有機(jī)化合物和堿溶液的腐蝕。換熱管可以比較薄,提高傳熱效果,設(shè)備體積和重量小。
1、材料選用
(1)管程走腐蝕性介質(zhì)的流程比較經(jīng)濟(jì)。在這種情況下?lián)Q熱管采用鈦管-管箱采用鈦復(fù)合鋼板或鈦襯里、管板可采用鈦復(fù)合鋼板或在鋼管板上襯6-10mm的鈦板,在結(jié)構(gòu)設(shè)計(jì)應(yīng)考慮殼體和管子之間的膨脹差問題。
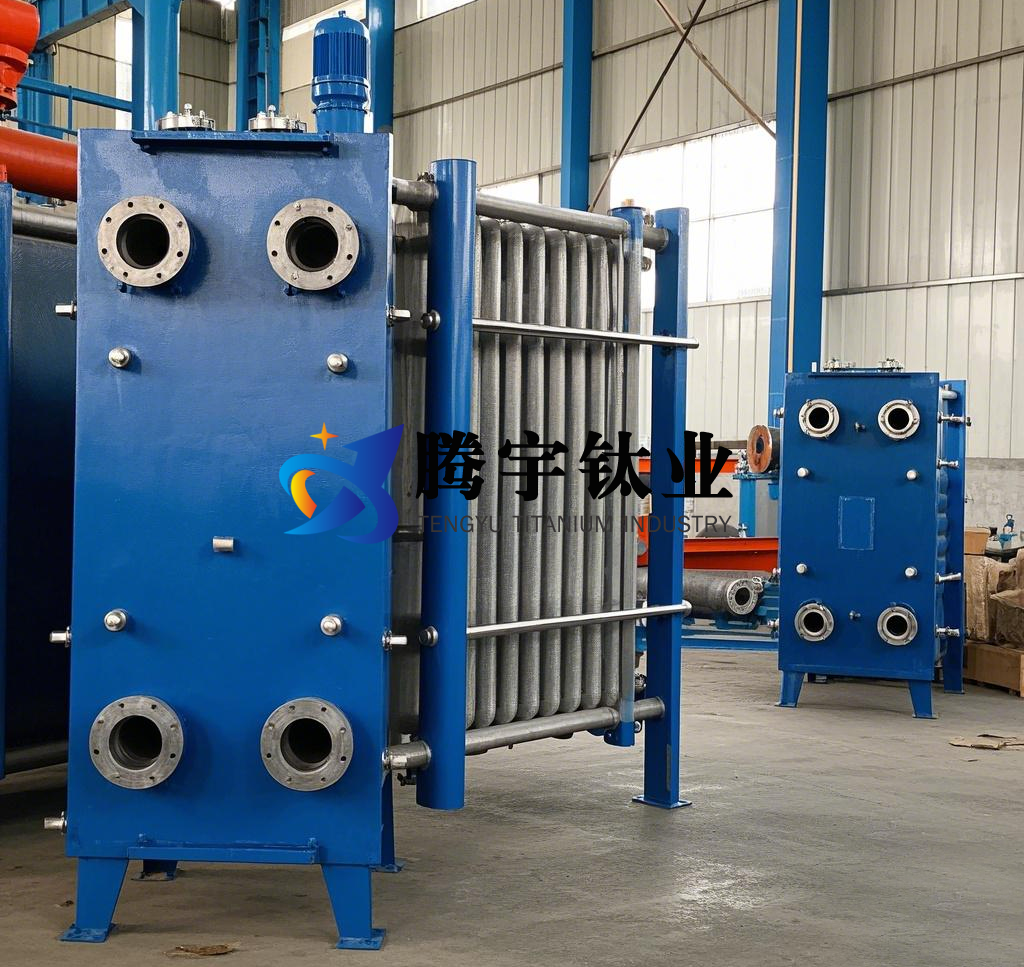
(2)復(fù)合管板結(jié)構(gòu)管板是鈦復(fù)合鋼板應(yīng)用的一個(gè)重要方面。由于管板操作條件苛刻,希望貼合率盡可能高。在這里順便介紹一下復(fù)合管板爆炸復(fù)合加工工藝,爆炸焊原理是在起爆過程中兩金屬產(chǎn)生高速傾斜碰撞,在碰撞點(diǎn)前形成足夠大的高壓區(qū)。這個(gè)高壓區(qū)的壓力超過-臨界壓力(大于材料屈服強(qiáng)度10倍左右)同時(shí),兩金屬碰撞時(shí),碰撞角必須超過某一臨界角度并把碰撞點(diǎn)的速度控制在亞音速范圍內(nèi),以產(chǎn)生噴射流破除和清潔金屬內(nèi)表面臟物,露出潔凈金屬在高壓作用下二金屬冶金結(jié)合在一起在高壓作用下二金屬冶金結(jié)合在一起。
(3)管子與管板連接形式
①脹接:脹接是靠管子的變形來達(dá)到密封合固緊的一種機(jī)械連接法。這種連接法受溫度限制比受壓力限制大。隨著溫度升高,管與管板剛性下降,熱膨脹應(yīng)力增大,引起接頭松動(dòng)。這一點(diǎn),對(duì)鈦制換熱器更為突出,因?yàn)殁伒牧W(xué)性能隨溫度變化較一般碳素鋼、低合金鋼哥更大。另一方面,工業(yè)純鈦在常溫下有低溫蠕變現(xiàn)象,在可能產(chǎn)生縫隙腐蝕的環(huán)境不宜采用。
②焊接:高溫度、壓力較高時(shí),焊比脹更能保證密封性,在高溫下,蠕變使脹接殘余應(yīng)力松弛,易造成泄漏,但焊接不能完全避免縫隙腐蝕。
③脹接加密封焊:這種連接適用復(fù)合管板,管子所承受載荷由脹接承擔(dān),密封焊只起加強(qiáng)密封作用,在可能產(chǎn)生縫隙腐蝕的環(huán)境中,應(yīng)采用這種連接方法。
根據(jù)上述優(yōu)點(diǎn):由于殼程走熱水,我裝置鈦換熱器采用是鈦管-管箱采用鈦復(fù)合鋼板,鈦列管與復(fù)合管板采用脹接加密封焊形式。
2、以往發(fā)生的故障及處理方法
2.1首次故障背景
在這臺(tái)換熱器投用的第一年就發(fā)生管程泄漏,經(jīng)檢查發(fā)現(xiàn)復(fù)合管板的鈦復(fù)合層有缺陷,造成管程泄漏。
檢修方案如下:更換二端復(fù)合管板,保留鈦列管。二端復(fù)合管板割除,相應(yīng)的鈦列管、碳鋼殼體根據(jù)管板厚度縮短150-200mm,盡量控制在160mm內(nèi),復(fù)合管板重新制作,列管與管板采用脹接加密封焊,殼體內(nèi)的折流板、定距管、拉桿等重新制作,殼體保留。
2.2二次故障背景
在使用二年后因密封面泄漏造成復(fù)合層分離。腐蝕原因:
因?yàn)殁亾Q熱器的管箱密封面的滲漏,帶有腐蝕性介質(zhì)的鹽酸自密封面處滲出,慢慢地滲入到鈦與鋼的結(jié)合部位,長(zhǎng)時(shí)間的腐蝕作用,使鈦與鋼的結(jié)合處產(chǎn)生腐蝕分離現(xiàn)象。如圖a所示:

檢修方案如下:上述腐蝕長(zhǎng)度約200mm,寬約20mm,深約30mm,共有四處這樣的腐蝕區(qū)域。設(shè)備左右復(fù)合管板復(fù)層與基層間的腐蝕區(qū),采用各鑲一同形狀的復(fù)合板(鈦-鋼),然后復(fù)層鈦與鈦之間倒坡口焊接,基層鋼與鋼之間倒坡口焊接(。維修前腐蝕區(qū)要加工成較規(guī)則形狀)。鑒于兩管箱鈦焊環(huán)密封面有腐蝕和脆化現(xiàn)象,該密封面鈦材已有縫隙腐蝕和吸氫現(xiàn)象,已無維修補(bǔ)焊的可能,更換材質(zhì)為TA10,該材質(zhì)耐縫隙腐蝕性能較好。如上圖b所示。
2.3本次故障背景
再使用了四年后,再次發(fā)生因密封面泄漏造成復(fù)合層分離,現(xiàn)象與第二次相同,復(fù)合板邊沿鈦與鋼的結(jié)合處產(chǎn)生腐蝕分離現(xiàn)象,兩管箱鈦焊環(huán)密封面有腐蝕和脆化現(xiàn)象,因生產(chǎn)檢修情況緊急,所以采用酚醛樹脂涂在密封面和墊片之間,在酚醛樹脂流動(dòng)狀態(tài)下上緊管箱的法蘭螺栓,待酚醛樹脂固化后投入生產(chǎn)使用,這是臨時(shí)措施。
為使在短時(shí)間內(nèi)對(duì)該換熱器進(jìn)行整修,為此事業(yè)部設(shè)備動(dòng)力部與設(shè)計(jì)制造單位協(xié)商在短時(shí)期內(nèi)完成較徹底的檢修,第一次的方案因復(fù)合管板的加工周期較長(zhǎng),以及費(fèi)用較貴(原因是鈦材近期漲幅過大),無法確保生產(chǎn)應(yīng)急;第二次的方案采用各鑲一同形狀的復(fù)合板(鈦-鋼),然后復(fù)層鈦與鈦之間倒坡口焊接,基層鋼與鋼之間倒坡口焊接。由于此臺(tái)換熱器此次復(fù)合板泄漏點(diǎn)就靠近上次返修鑲復(fù)合板部位,而且上次腐蝕長(zhǎng)度約200mm,寬約20mm,深約30mm,共有四處這樣的腐蝕區(qū)域,此方案成功的可能性已無。
3、此次檢修的方案及對(duì)故障原因分析及措施
由于反復(fù)出現(xiàn)因密封面泄漏造成復(fù)合層因腐蝕分離,通過對(duì)現(xiàn)場(chǎng)目前的工藝條件與初步設(shè)計(jì)的工藝條件進(jìn)行比較,發(fā)現(xiàn)由于裝置進(jìn)行改擴(kuò)建,工藝配套的輸送泵的揚(yáng)程發(fā)生變動(dòng),變動(dòng)情況如下:
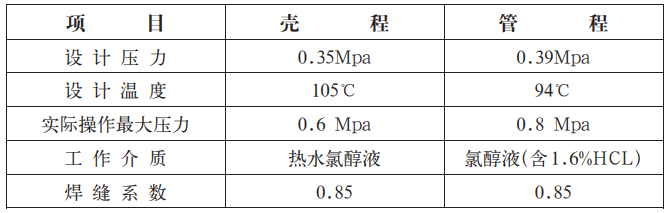
項(xiàng)目因此對(duì)該換熱器的法蘭強(qiáng)度進(jìn)行重新校核,發(fā)現(xiàn)密封面泄漏造成的實(shí)際因素。下列是校核過程:
除管箱法蘭校核不合格外,由于聚四氟乙烯墊片壓不緊形成縫隙,易產(chǎn)生縫隙腐蝕,產(chǎn)生原因分析:用聚四氟乙烯墊墊片又過寬,都碰在管板凸面上,同時(shí)發(fā)現(xiàn),管板泄漏較重的密封面墊片上的壓痕深淺明顯不同,說明連接法蘭時(shí)緊固螺栓用力不均,造成密封墊片上受力大小不同,使墊片與管板之間的狹縫間隙的幾何尺寸處在產(chǎn)生較大腐蝕速度的敏感區(qū)域,一部分物料滲入并維持靜滯狀態(tài),與鈦的鈍化膜發(fā)生化學(xué)反應(yīng),使鈍化膜破裂,在縫隙中,由于氧化膜被破壞,滲入的液體又阻礙氧(或氧化劑)進(jìn)入,這樣由于縫內(nèi)外氧濃差造成宏觀電池,生成TiH2;此外,由于物料中含有Cl-離子,從縫外向縫內(nèi)擴(kuò)散造成濃縮,并與水解反應(yīng)形成的氫離子生成鹽酸,加速鈦的腐蝕,這樣不斷循環(huán),縫內(nèi)金屬鈦不斷溶解,產(chǎn)生較嚴(yán)重的縫隙腐蝕。泄漏的介質(zhì)中含有鹽酸,與復(fù)合面上的基層材料發(fā)生反應(yīng),隨著時(shí)間的推移,腐蝕長(zhǎng)度、深度不斷擴(kuò)大,就這樣形成了腐蝕帶。所以需采用堅(jiān)固的法蘭和較大的螺栓來加強(qiáng)法蘭密封,另外采用抗縫隙腐蝕較好的鈦鈀合金來做密封面材料,鈦鈀合金具有三個(gè)優(yōu)點(diǎn):對(duì)稀鹽酸和稀硫酸的耐蝕性比純鈦高,這種合金改善了工業(yè)純鈦在還原性介質(zhì)中的耐蝕性能,如它在室溫的10%硫酸、10%的鹽酸以及中等濃度的甲酸和檸檬酸中均具有較好的耐蝕性能,而且它保持了純鈦的耐硝酸、鉻酸等氧化性介質(zhì)的耐蝕性能;具有較好的耐縫隙腐蝕能力;吸氫能力小,不宜產(chǎn)生氫脆,表面生成的氧化膜具有較高的抗氫滲透能力。
Ti-0.3Mo-0.8Ni合金的加工性能、焊接性能接近純鈦,而在200-300℃下強(qiáng)度較純鈦高1.5-2倍。
為此我們提出一個(gè)較為合理又簡(jiǎn)便實(shí)用的檢修方案:如圖c所示:
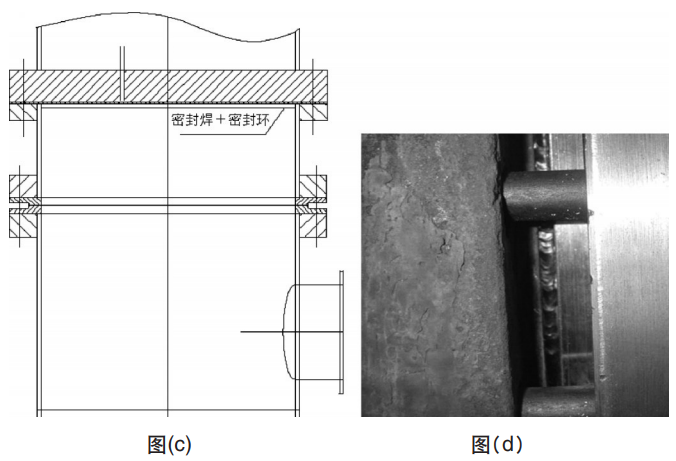
如圖,增加一筒節(jié),筒節(jié)內(nèi)有兩塊(TA2)8mm隔板,筒節(jié)材料可以用復(fù)合板或純TA2,筒節(jié)一端和殼程復(fù)合管板密封面連接處焊死,由于鈦復(fù)合面由原來單純受壓狀態(tài),經(jīng)過與短節(jié)焊接后成受拉伸狀況,所以對(duì)焊接面的法蘭螺栓要全部帶緊,增加對(duì)鈦復(fù)合面的預(yù)緊力,防止鈦復(fù)合面剝離。如圖(d)所示:
另一端與管箱活套法蘭連接,法蘭厚度從原設(shè)計(jì)60mm增加到70mm.,焊環(huán)采用鈦鈀密封環(huán)。對(duì)原管箱的焊環(huán)更換成鈦鈀材料,活套法蘭增厚為70mm。
4、結(jié)論
經(jīng)過上述的搶修,對(duì)設(shè)備殼程和管程進(jìn)行水壓試驗(yàn),壓力為實(shí)際操作最大壓力的1.25倍,分別為0.75Mpa和1Mpa,經(jīng)試驗(yàn)合格后即投入生產(chǎn)運(yùn)行,目前運(yùn)行正常。證明本次檢修方案的合理性經(jīng)得起考驗(yàn)。
參考文獻(xiàn):
[1]曾亮,周春玉,張東,相變材料導(dǎo)熱性能強(qiáng)化的研究發(fā)展,材料科學(xué)與工程,上海,2010.
[2]王志魁,《化工原理》,化學(xué)工業(yè)出版社.
[3]錢頌文,換熱器設(shè)計(jì)手冊(cè),2007.
[4]張平亮,新型換熱器及其技術(shù)發(fā)展,煉油技術(shù)與工程,2007.
[5]廖傳華,史勇春傳熱過程與設(shè)備{M},北京:中國(guó)石化出版社,2008.
[6]史美中,王中錚.熱交換器原理與設(shè)計(jì){M},南京:東南大學(xué)出版社.
作者簡(jiǎn)介:郭洋洋,男,(1984-),中國(guó)石化上海高橋石油化工有限公司,從事設(shè)備材料運(yùn)行管理及采購的質(zhì)量控制工作。
相關(guān)鏈接